In-Depth: Realising Breguet’s Dream of the Natural Escapement
Two hundred years later, it comes true.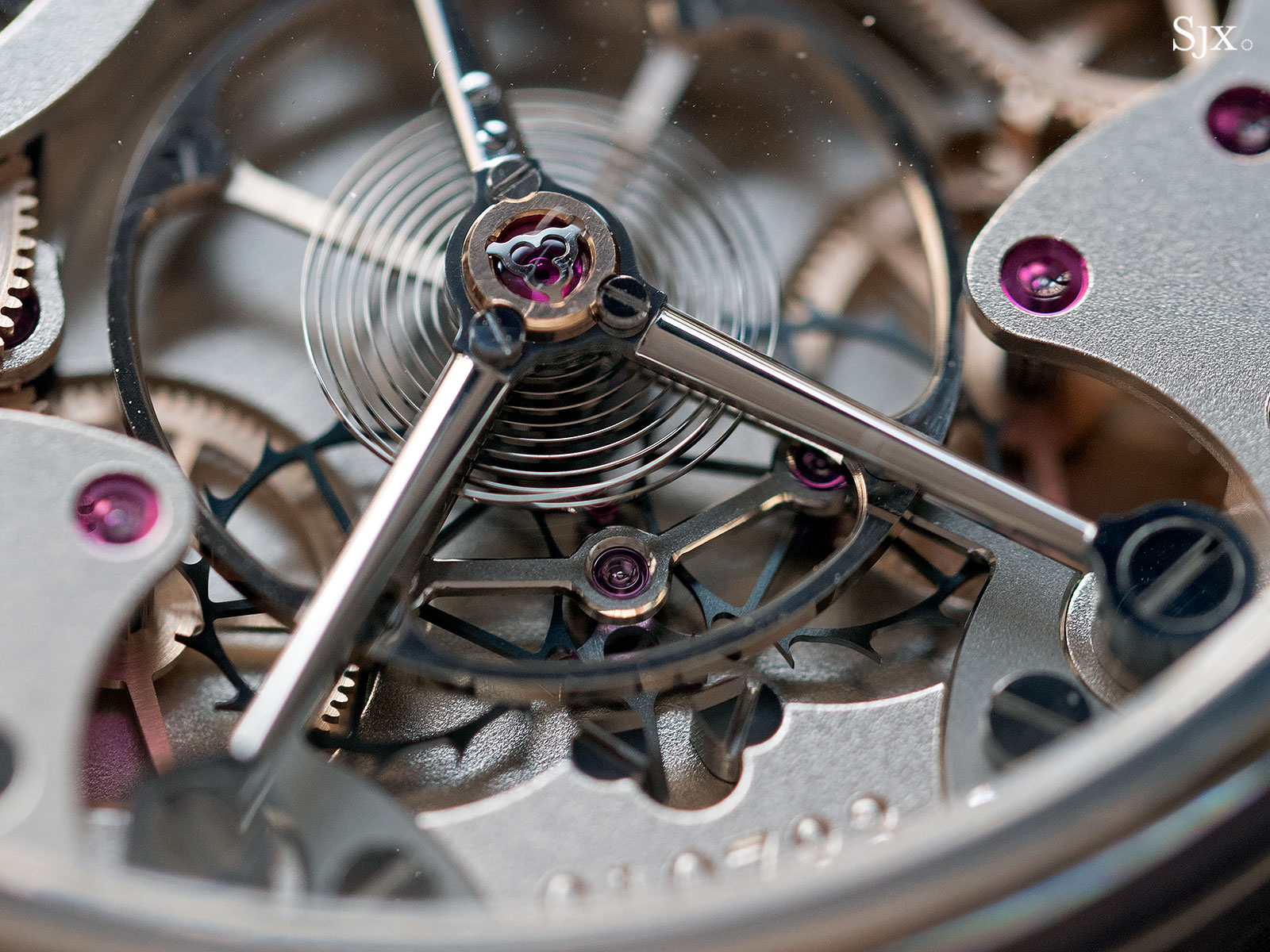
Abraham-Louis Breguet’s contributions to horology are as numerous as they are fundamental. Practically every avenue of watchmaking is built on the foundations he laid down, from the perpetuelle self-winding mechanism to pare-chute shock-protection for balance pivots.
But most famous of all was the tourbillon, patented in 1801. It was crucial to the precision of mechanical pocket watches and clocks, the only kinds of timepieces in use then, which normally sat in an upright, vertical position.
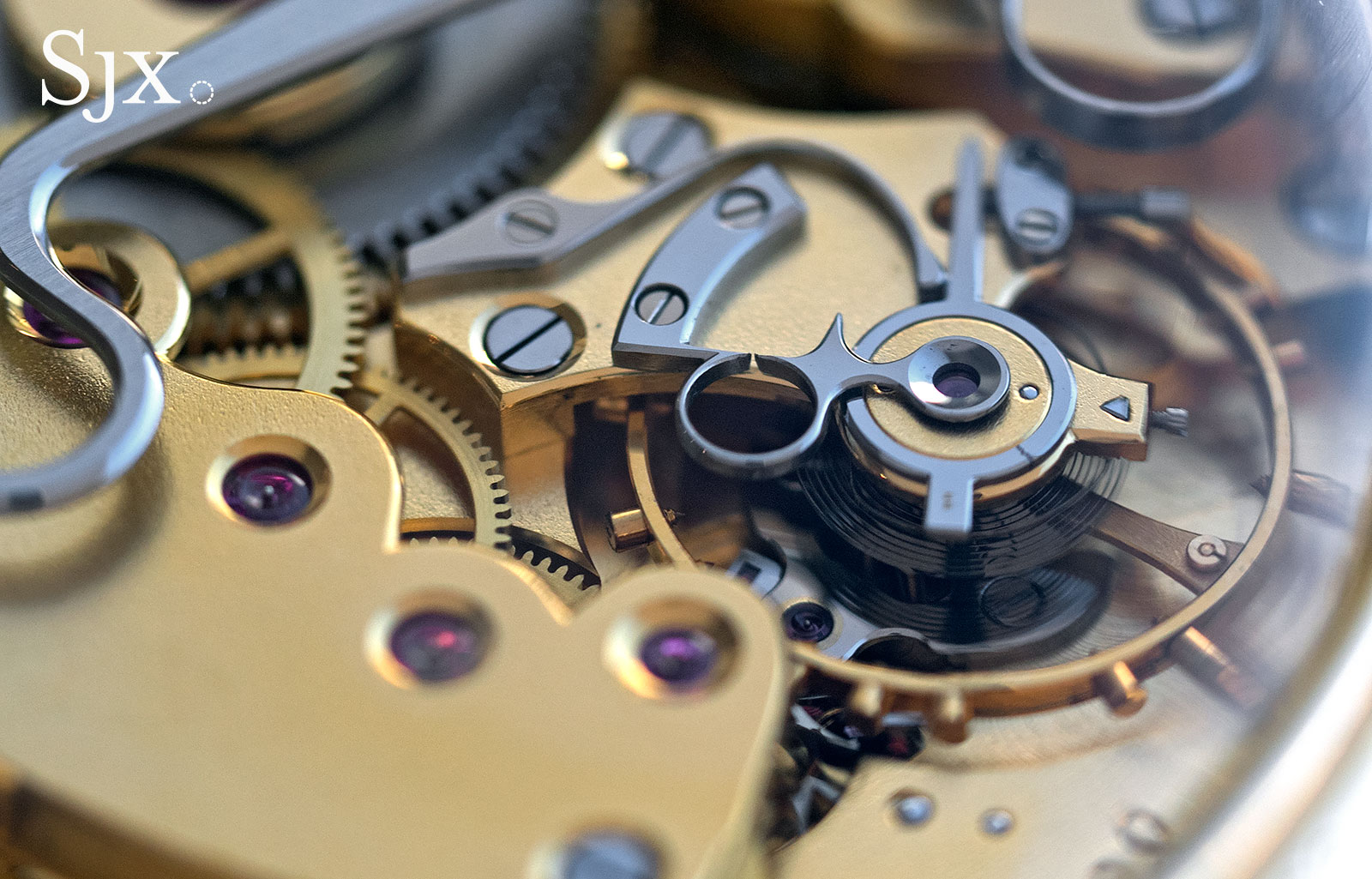
The Breguet Souscription pocket watch of the 1990s that replicated the 19th century originals, right down to the pare-chute escapement
The tourbillon, however, was not Breguet’s only effort in improving chronometric performance. Prior to the tourbillon, he created the lesser known but more elegant echappement naturel, or natural escapement, in 1789.
It was a double-wheel chronometer escapement that in theory, needed no oil. Breguet managed to incorporate it into just 20 pocket watches, but serial production of the natural escapement ultimately eluded him as its design had inherent shortcomings – primarily backlash in the motion of its wheels – that made it impossible to commercialise. The idea was ahead of its time, and it would take some 200 years before technology made the natural escapement feasible.
The concept of natural escapements continues to fascinate watchmakers, many of whom have conceived modern-day descendants, the most recent of which is the Charles Frodsham Double Impulse Chronometer, launched just last year. Thanks to modern manufacturing and materials, today’s natural escapements are as varied as they are intriguing – and they function properly. But before proceeding into the current crop of natural escapements, it’s important to understand the two escapement types that illuminate the reasons why Breguet invented the natural escapement in the first place.
The self-starting escapement
The first is the lever, or in-line, escapement that was invented by English clockmaker Thomas Mudge (1715-1794) in 1755. Through an evolution over 250 years, this has become the most common form of escapement today, used in the vast majority of mechanical watches on the market. In fact, it’s synonymous with Swiss watches, and is sometimes known as the Swiss lever escapement.
It gets its name from the jewelled pallet fork that sits between the escape and the balance wheel. While earlier escapements, including the verge and cylinder escapements, rely on the escape wheel to impulse the balance directly, the lever escapement has the pallet fork as an intermediary between the escape and balance wheel.
The below animation shows a typical lever escapement design. Power is released from the mainspring and drives the escape wheel. It pushes against the pallet fork – specifically, the two pallet jewels set in the tips of the pallet fork, which has a specific trapezoidal geometry. That is an important feature of the design, because the sloped ends of the pallets allow for a sliding motion of the escape wheel against the pallet fork.
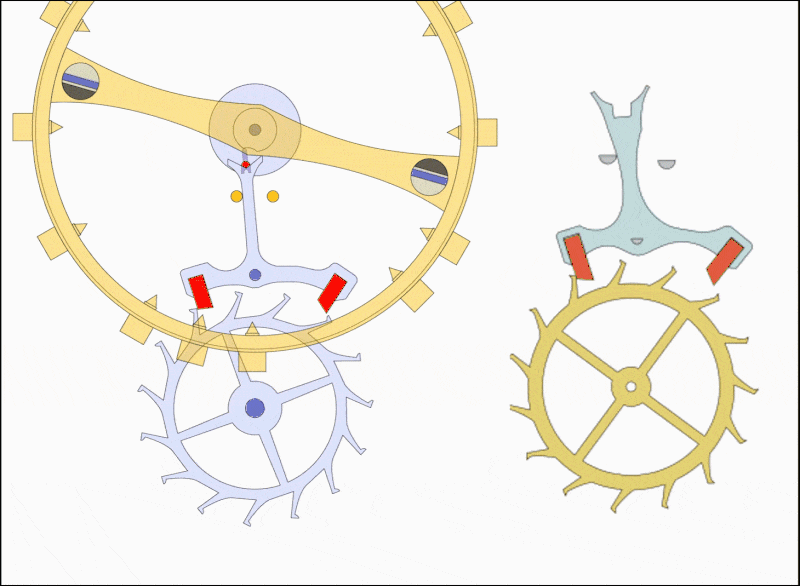
Animation of the lever escapement. Image – Wikipedia
The sliding motion unavoidably creates friction, but is a necessary evil as it is this very action that transmits energy from the escape wheel, through the pallet fork, to the balance wheel to get it oscillating back and forth. The characteristic “tick” and “tock” of a mechanical movement arises from the pallet fork jewels sequentially locking and unlocking the teeth of the escape wheel every cycle.
This design is simple, robust, and reliable enough, which explains its ubiquity. More important is the design’s inherent ability to self-start. All that is needed is a light shake to start the balance wheel oscillating, which in turn drives the pallet fork and the escape wheel.
However, the primary concern here is lubrication – the sliding motion of the pallet jewels is a major source of friction.
Consider a 2.5Hz watch – it beats 18,000 times an hour, or 432,000 times a day. That is 216,000 “ticks” and 216,000 “tocks” daily, which is also the number of times the sliding motion occurs, hence the need for sufficient lubrication.
Prior to the invention of synthetic lubricants, animal fat or derivatives were used, but such natural lubricants deteriorated quickly, sometimes within a matter of months. This issue gnawed at the genius of Breguet, to which he famously opined, “Give me the perfect oil, and I will give you the perfect watch.”
Lubrication-free
In that regard, there is a superior escapement, one that needs little to no lubrication – the detent escapement. Interestingly, it was invented before the lever escapement, in 1748, by French clockmaker Pierre Le Roy (1717–1785), then refined by English watchmakers John Arnold and Thomas Earnshaw.
Put simply, the detent escapement differs from the lever escapement as it utilises a pivoted detent blade instead of a pallet fork. While the lever escapement has two impulses per cycle – the “tick” and “tock” – the detent escapement only gives impulse to the balance wheel in one direction.
Referring to the below diagram, the detent spring is akin to a one-way “trapdoor” – it allows the balance wheel to swing freely clockwise past the “trapdoor”, but gets impulsed counterclockwise, which in turn unlocks the escape wheel one tooth forward.

Thomas Earnshaw’s version of the detent escapement. Diagram – Wikipedia
Unlike the lever escapement, the geometries involved in the detent escapement are quite ideal – as the impulse comes directly from the escape wheel almost without any sliding friction involved. In an era where lubricants deteriorated quickly, this was ideal since none of the impulsing surfaces needed lubrication in theory.
Alas, the design has one major shortcoming that the lever escapement does not suffer from: poor shock resistance.
The balance wheel needs to swing a large angle to a ready position (clockwise above) to get past the “trapdoor”, before gaining enough momentum to unlock the detent (counterclockwise above), releasing the escape wheel. During this period, any shocks may disrupt this momentum, thus stopping the watch. Additionally, this also means the escapement is not self-starting from a stationary position; a fairly large external force is needed to start the balance wheel.
Both these weaknesses explains why detent escapements are found in antique clocks and watches, but disappeared once wristwatches became the norm in the 20th century.
United as one, but…
Breguet (1747-1823) presumably spent a great deal of time pondering if it was possible to combine the self-starting capability of the lever escapement and the frictionless operation of the detent escapement, and conceived the natural escapement.
The basic principle was to mirror the detent escapement – keeping the detent in the centre while doubling the escape wheels – so a release occurs in each direction. The design is reminiscent of the lever escapement, which can be released in either direction.
The mechanism required two escape wheels, both driven together in opposite directions by meshing gear teeth. In the below image, escape wheel A is powered by the mainspring and gear train, while escape wheel B is driven by wheel A. Meanwhile, the escape wheel teeth responsible for locking and releasing the detent are now positioned vertically relative to the plane of the wheel, much like the “pillars” on a column wheel.
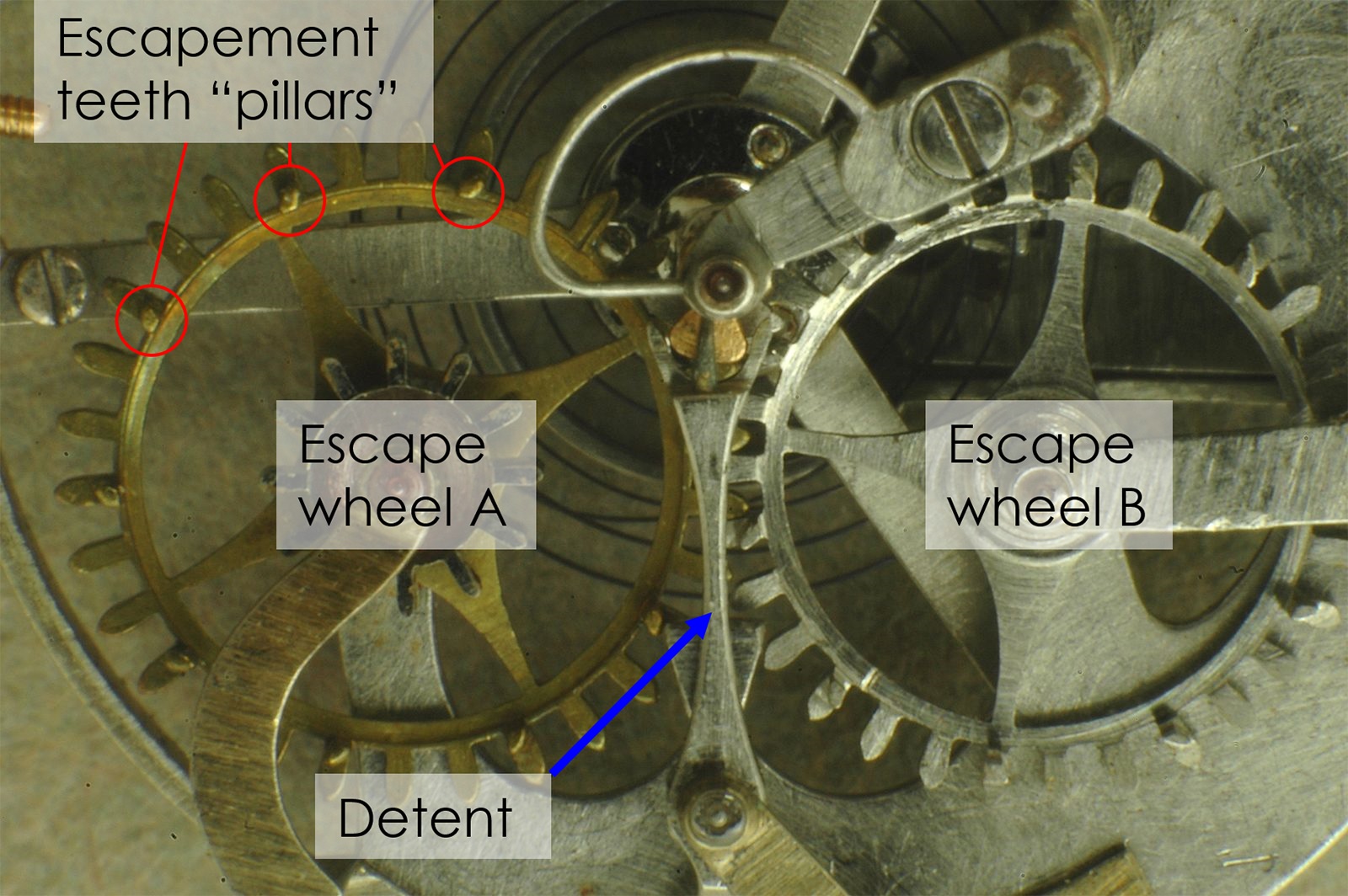
One of the earliest natural escapements, in Breguet pocket watch number 1135. Photo – Wikipedia
So, did Breguet bottle lightning with the natural escapement?
Not quite – the design had one shortcoming, a result of technological limitations at the time. Tolerances between the two escape wheels had to be tight, otherwise the driven escape wheel B suffers from “play” between the gears, resulting in backlash. This was a major issue, as the play results in variable impulse to the detent, and in extreme cases, stop the mechanism. Conversely, overly tight meshing, somewhat ironically, results in high friction between both escape wheel teeth – a disastrous outcome since the escape wheels are the fastest rotating gears in the going train.
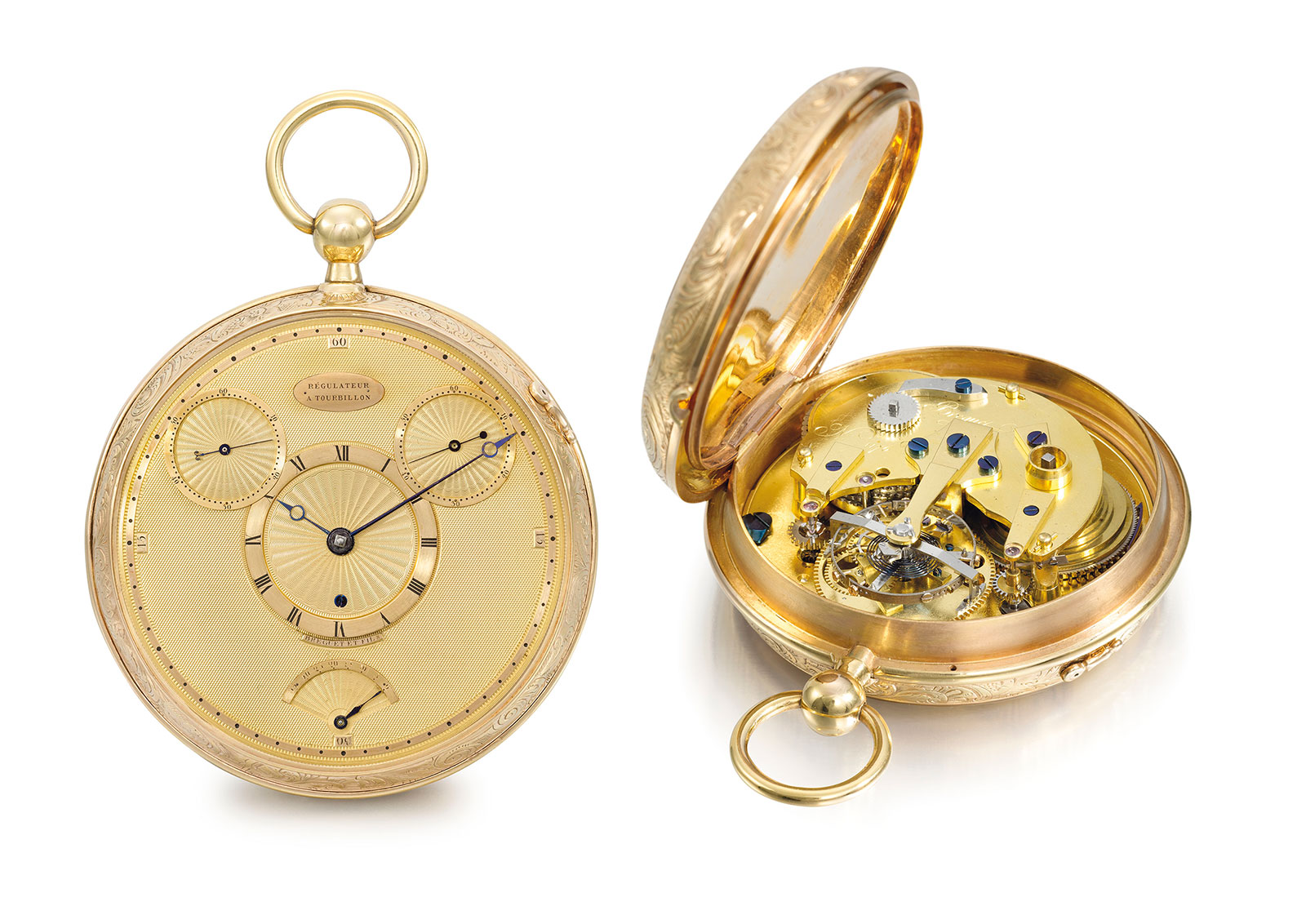
Breguet watch no. 1176 with a natural escapement and a four-minute tourbillon, now in the company’s collection. Photo – Christie’s
Breguet made several revisions to the natural escapement and installed it in 20 pocket watches, the first in 1802 and the last in 1822, a year before his death. Some examples have are well preserved and known, the most famous being pocket watch no. 1176 that was sold at Christie’s in 2014 for 821,000 Swiss francs and now resides at the Breguet museum.
He also used the natural escapement in several marine chronometers and clocks. However, due to the difficulty of manufacturing the escapement, it was not commercially viable and he focused his efforts on improving the lever escapement instead. Most attempts by other watchmakers to improve the natural escapement came to a halt by the end of 19th century.
An English solution
Breguet’s troubles with the escapement, however, did not deter a self-taught English watchmaker from devising his own solution, decades later. He was George Daniels (1926-2011).
Daniels ardently pursued escapement innovation, with his best-known invention being the Co-Axial, which was adopted by Omega and now ticks away in hundreds of thousands of watches. Coincidentally, the Co-Axial escapement was motivated by the same desire that fuelled Breguet’s invention – mitigating the sliding friction of regular escapements. Prior to its conception, however, Daniels attempted to improve Breguet’s natural escapement.
And so he did, starting with his fifth pocket watch, and most famously with the two subsequent watches – the Space Traveller I and Space Traveller II. The former was just sold in London a month ago for US$4.56m, while the latter is now on show at the Clockmakers’ Museum inside London’s Science Museum.
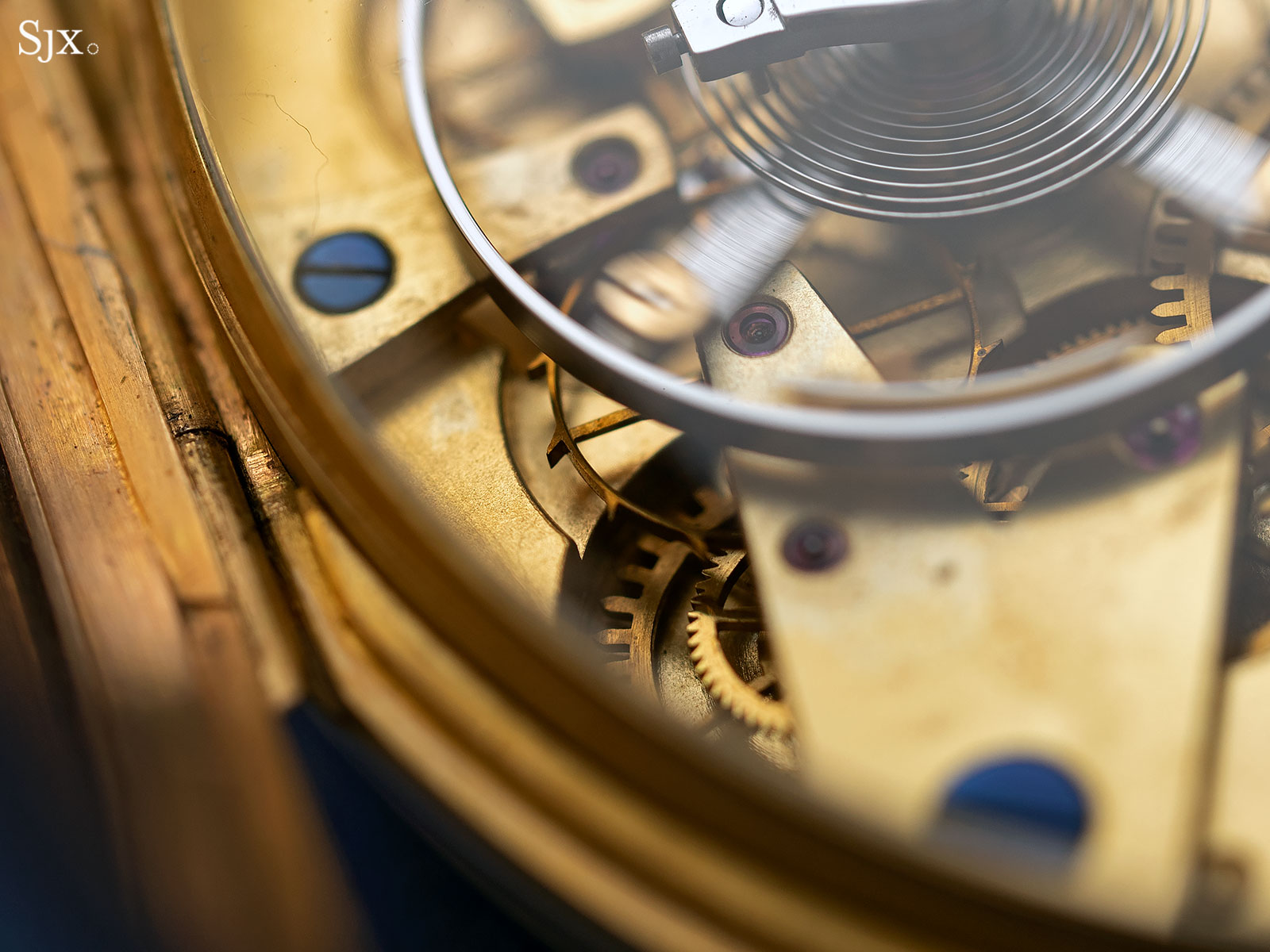
One of the two escape wheels in the Space Traveller I
Daniels, however, tweaked Breguet’s concept in order to make it functionally reliable, removing the direct connection between the two escape wheels. Instead of having one escape wheel drive the other, he gave each escape wheel its own power supply, with each having its own mainspring and gear train. This setup drives each escape wheel independently, which resolves Breguet’s original problem of play between the escape wheels and prevents the mechanism from seizing up. This also meant that instead of escape wheels with vertical teeth, or pillars, as in Breguet’s original design, Daniels was able to use conventionally shaped escape wheels driven by regular pinions.
But the Daniels double wheel escapement, as he named it, was a relatively bulky and expensive solution, since it is essentially two movements in one watch. So Daniels naturally wondered if he could make more out of the concept, and hit on the idea of having each gear train indicating a different type of time – literally two different movements in one watch.
And that’s what he did, creating a watch with the right sub-dial displaying mean solar time, and the left indicating sidereal time. Because the watch could tell the time on Earth and also for someone journeying the cosmos, Daniels named it the Space Traveller, which was also a reference to the Moon landing of 1969.
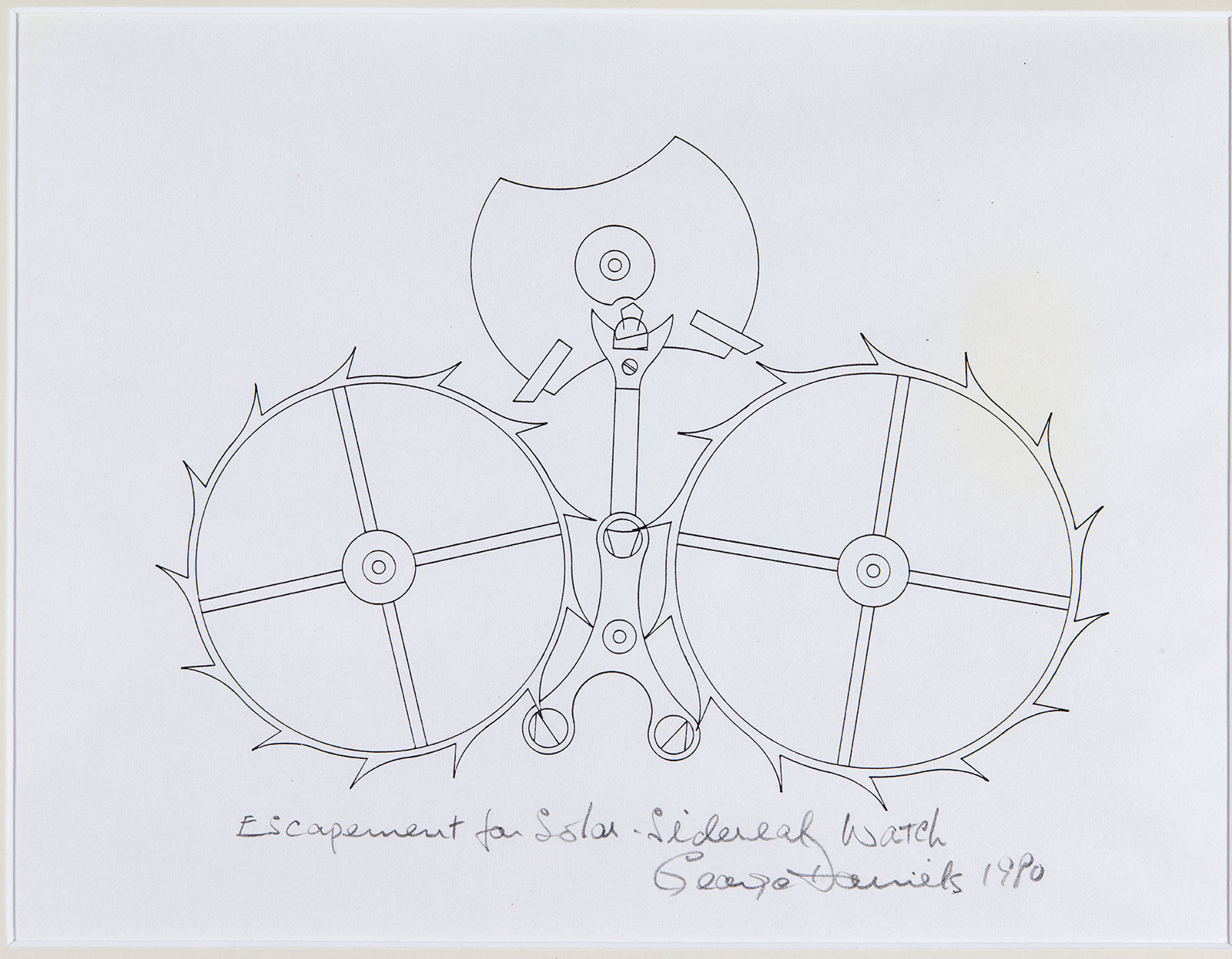
The asymmetrical escape wheels of the Space Traveller, drawn by Daniels in 1980. Photo – Sotheby’s.
A quirk of the Space Traveller was that each escape wheel needed different number of teeth, with the mean solar time wheel having 13 teeth and the sidereal time, 14. Though uncommon, that wasn’t a new idea – Breguet himself had observed that the second driven escape wheel in the natural escapement could be smaller to reduce its weight and inertia, as long as the number of impulse teeth was proportionally reduced.
Furthermore, something fascinating occurs under the dial of the Space Traveller, due to the two time displays with independent gear trains. Since each escapement is released in alternate intervals as the balance wheel oscillates, it can be observed that both second hands take alternating turns to move, each ticking forward at a leisurely 18,000bph, one after the other.
English, again
While the most famous, Daniels was not the only English watchmaker working on the natural escapement. A younger but equally capable English watchmaker, Derek Pratt (1938-2009), had also undertaken the challenge of creating a working natural escapement. Unsurprisingly, both Daniels and Pratt were friends, and spoke on the phone almost weekly.
Pratt, however, approached the problem differently than Daniels, and did not use two separate gear trains. His solution took inspiration from another invention by Breguet – the tourbillon. To understand Pratt’s invention, remember that there are two escape wheels in a natural escapement, with both rotating in opposite directions.
Pratt’s observation was that a tourbillon cage rotates on a fixed fourth wheel, and contains the escapement within. The cage essentially “drags” along the escape wheels as it rotates, and the escape wheel is released in sync with the pallet fork and balance wheel. But if two escape wheels were used in a tourbillon, they would both rotate in the same direction, which simply wouldn’t work as they need to rotate in opposite directions in a natural escapement.
Thus, Pratt had an epiphany: what if a fixed, internal gear ring was also installed? Such a ring, which sits around the fourth wheel, would allow both escape wheels to be driven separately, with the left being driven by the fourth wheel and rotating anticlockwise, while the right driven by the internal gear ring and rotating clockwise. The minimal number of additional moving parts or wheels minimises gear tolerances enough for the escapement to work, and work it did.
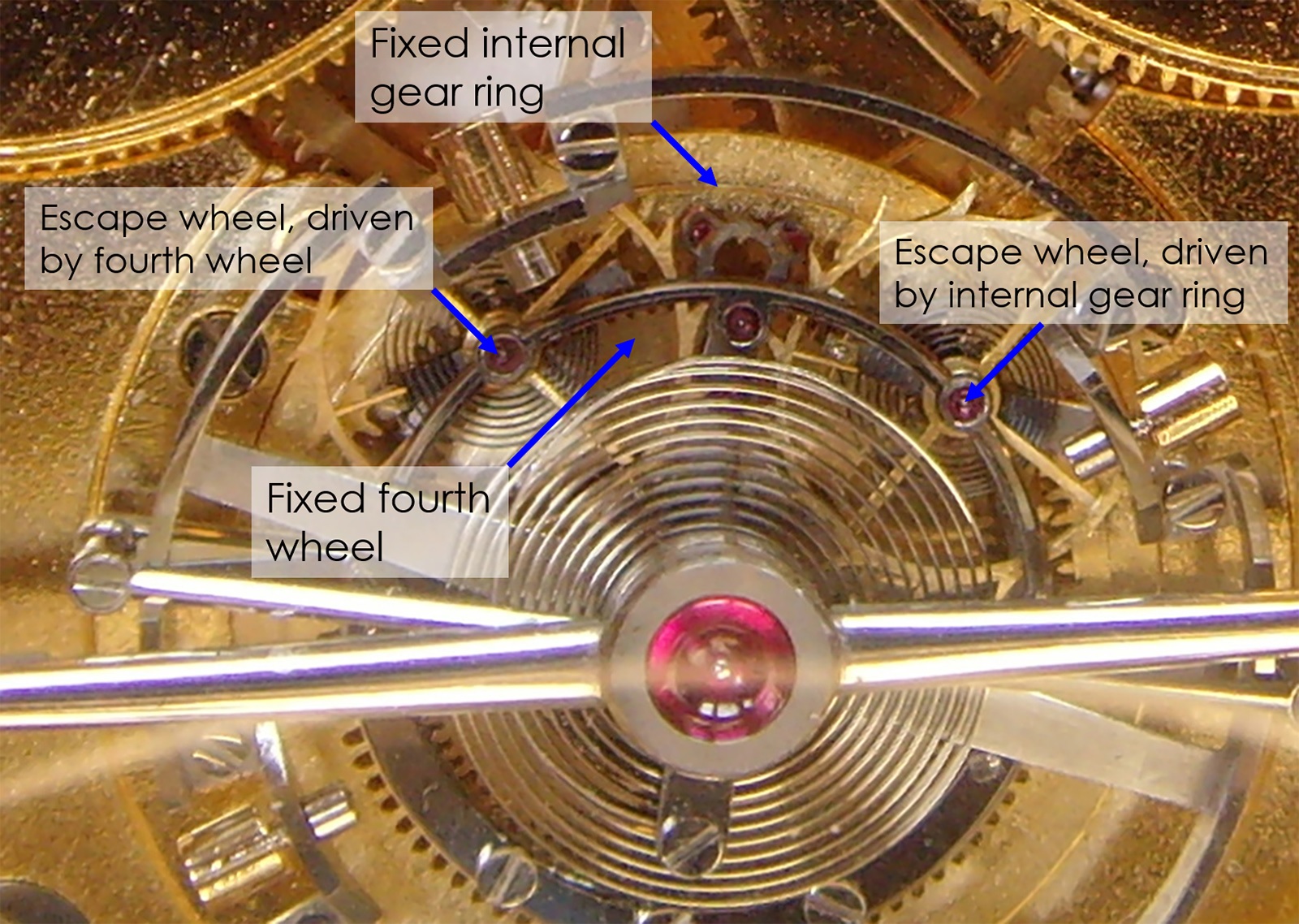
The twin escape wheels found in the Double-Wheel Remontoir Tourbillon
That led to the Double-Wheel Remontoir Tourbillon of 1997, which was a pocket watch conceived for perfect chronometric performance. In addition to the natural escapement in the tourbillon, Pratt went a step further by integrating separate remontoir springs into each escape wheel – making it a double constant force escapement. The remontoir springs regulate the torque from the twin mainspring barrels, and provide a relatively constant force to each escapement, resulting in better isochronism and better timekeeping.
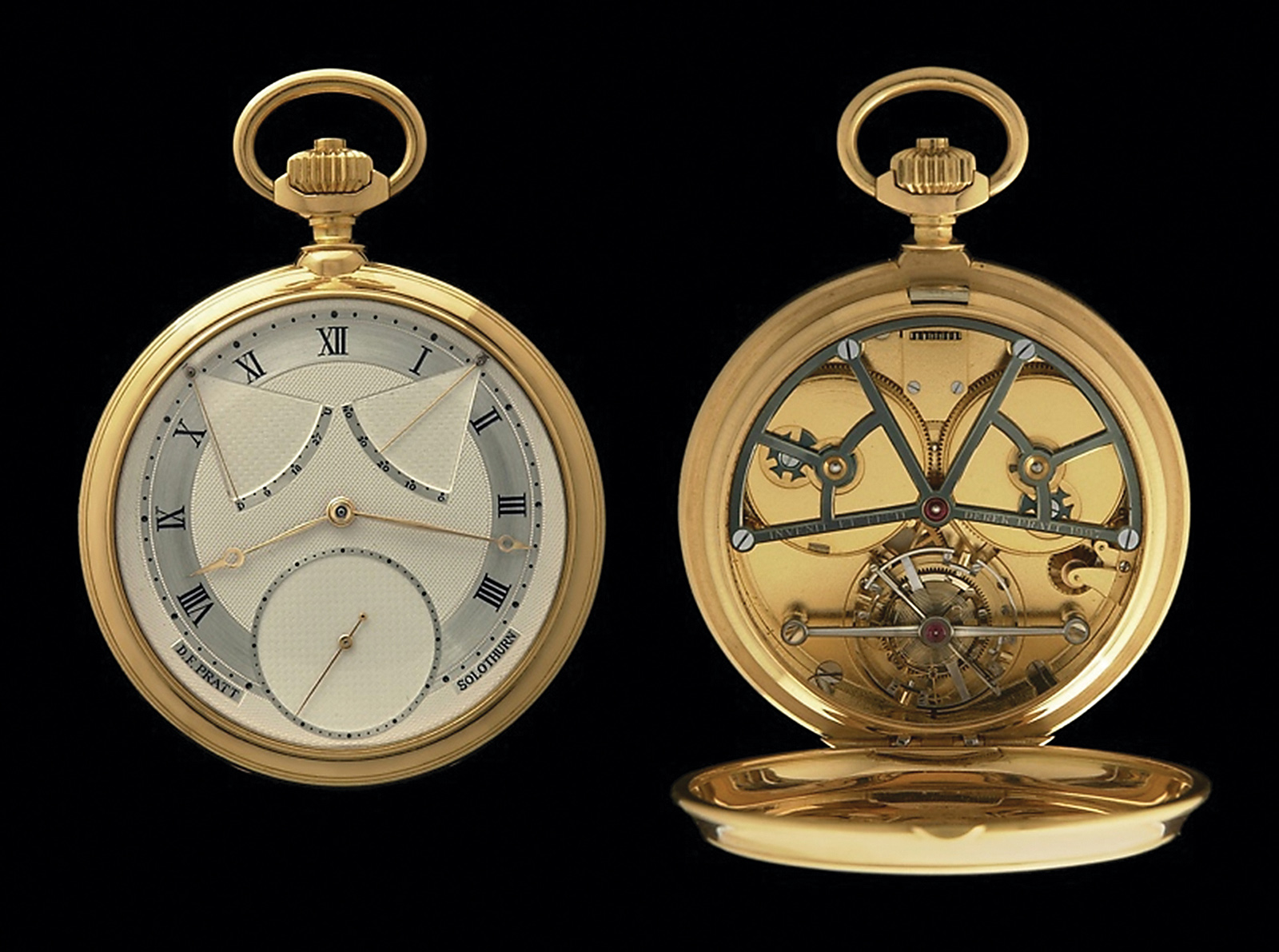
Derek Pratt’s Double-Wheel Remontoir Tourbillon
But Pratt’s watch was still a pocket watch; his invention was was too large to be adapted into a wristwatch, although on paper it was theoretically possible and something Pratt had dreamed of until his untimely death in 2009.
Modern-day ideas
Present day technology has rendered Breguet’s natural escapement feasible enough to be serially produced in wristwatches. The two crucial factors behind its realisation is the use of modern materials like silicon and nickel phosphorus, and the high precision of various specialised manufacturing methods.
The two factors are in fact inextricably linked – silicon parts are made by a subtractive etching process called deep reactive-ion etching (DRIE), while precision metal parts are additively formed in microscopic moulds using the Lithographie, Galvanoformung, Abformung (LIGA) process. Meanwhile, traditional movement components are made using computer numerical control (CNC) or wire erosion machines, which allows for milling or cutting of parts to precise tolerances.
Although variants of the natural escapement are found in a great variety of modern wristwatches, some are more important in innovation and execution, but all are directly evolved from the natural escapement. Modern interpretations of Breguet’s escapement can be classified into two categories: those that use only traditional metal alloys, and those that incorporate silicon components.
Ulysse Nardin Dual Direct Escapement (2001)
The unveiling of the Ulysse Nardin Freak in 2001 was revolutionary in many ways – it was timepiece without a dial, hands, or crown. Instead, the entire movement is a carrousel doubling as the minute hand, with a separate plate underneath acting as the hour hand. (Tech geeks debate if the Freak is indeed a carrousel, as there is only one active pinion driving the main carriage against a fixed peripheral rack, but that is an argument for another article.)
While the strongly visual layout of the movement is what made the Freak famous, the escapement that made its debut inside the watch was equally groundbreaking. Named the Dual Direct Escapement, it was the first serially produced wristwatch that incorporated a variant of Breguet’s natural escapement. It was possible thanks to the use of silicon for both escape wheels – which also put the Freak in the history books as the first wristwatch to use silicon parts. The silicon wheels were supplied by Centre Suisse d’Electronique et Microtechnique (CSEM), a Swiss research institute that developed silicon parts with the backing of a consortium made up of Rolex, Swatch Group, Patek Philippe and Ulysse Nardin.
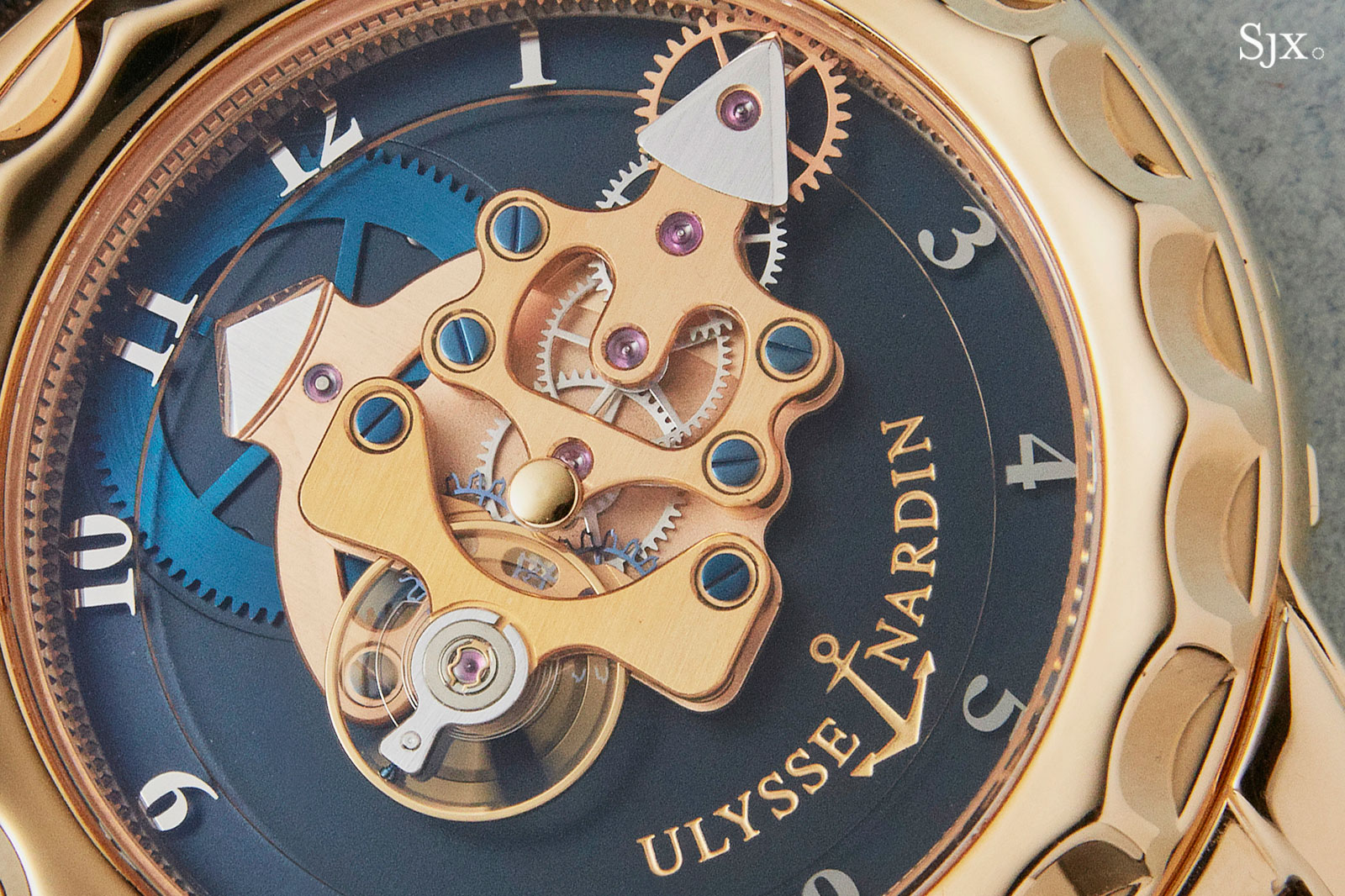
The original Freak of 2001, with a second-generation dual wheel escapement that has different teeth geometry from the first generation
The use of silicon was not merely for the sake of boasting about an exotic material. Silicon components are inherently able to achieve the precision required by the natural escapement, thanks to the high resolution of the DRIE process used to produce them.
But in the early years of silicon movement parts – this was almost 20 years ago now – the limitations of DRIE meant the escapement design had to be adapted in order to be viable. Consider that Breguet’s original design required escape wheels with complex geometry, with vertical pillars sticking out of the plane of the gears. In its infancy, silicon parts were mostly etched as as flat, planar components. It would be only years later that three-dimensional silicon parts would emerge, when DRIE production of components with multiple planes became widespread.
As a workaround to that limitation, the Dual Direct Escapement in the Freak ingeniously integrated all the functional components into a single plane. Observe the two meshing escape wheels below have 25 teeth each. Most of the teeth have flat tips, but every fifth tooth protrudes outward slightly to a pointed tip – these serve as the raised “pillars” of Breguet’s original escape wheel design. These protrusions are just long enough to contact a compact, pivoting stopper (2), while the other shorter teeth clear past it.
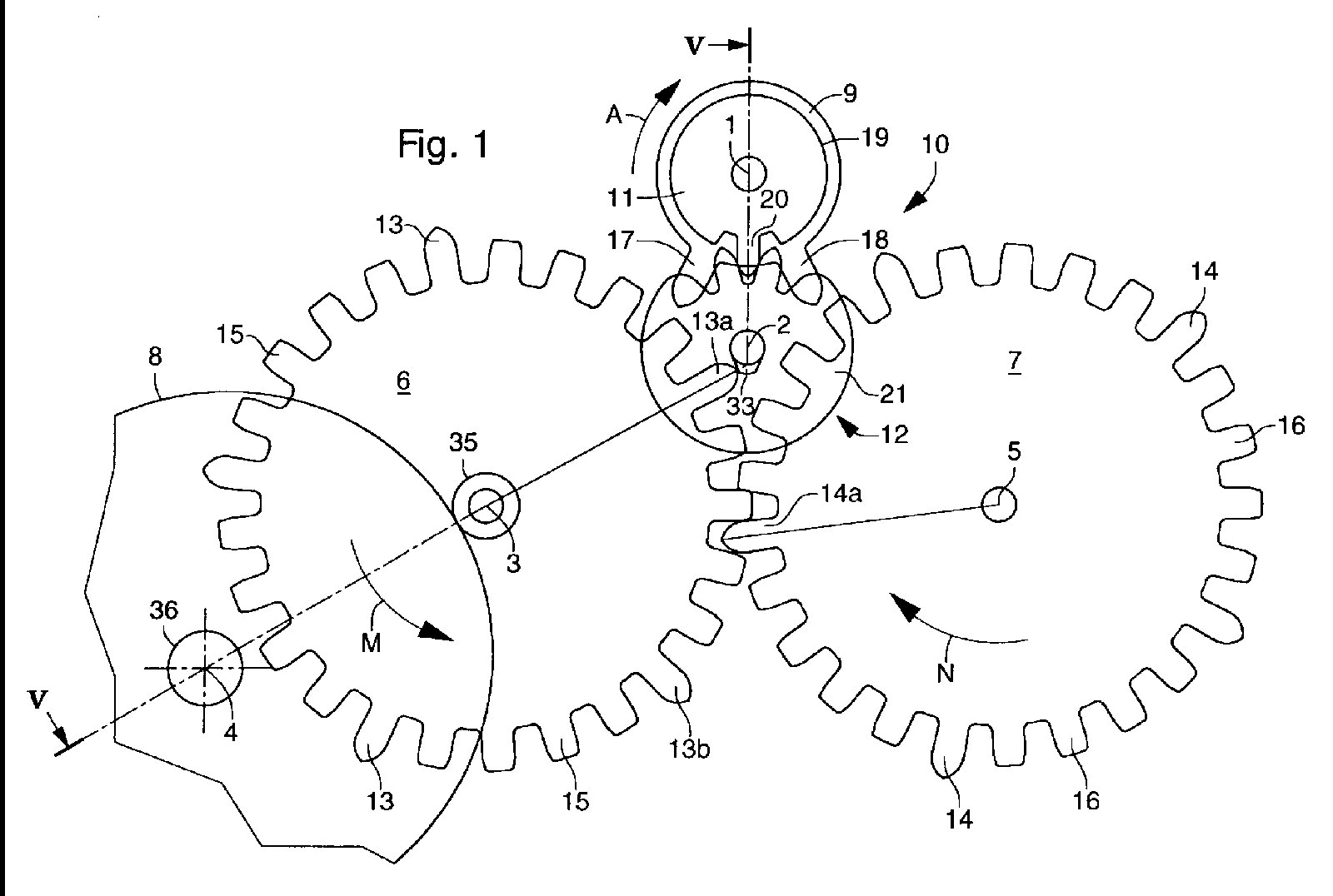
The Ulysse Nardin Dual Direct Escapement, as detailed its 2000 patent. Source – European patent EP1041459A1
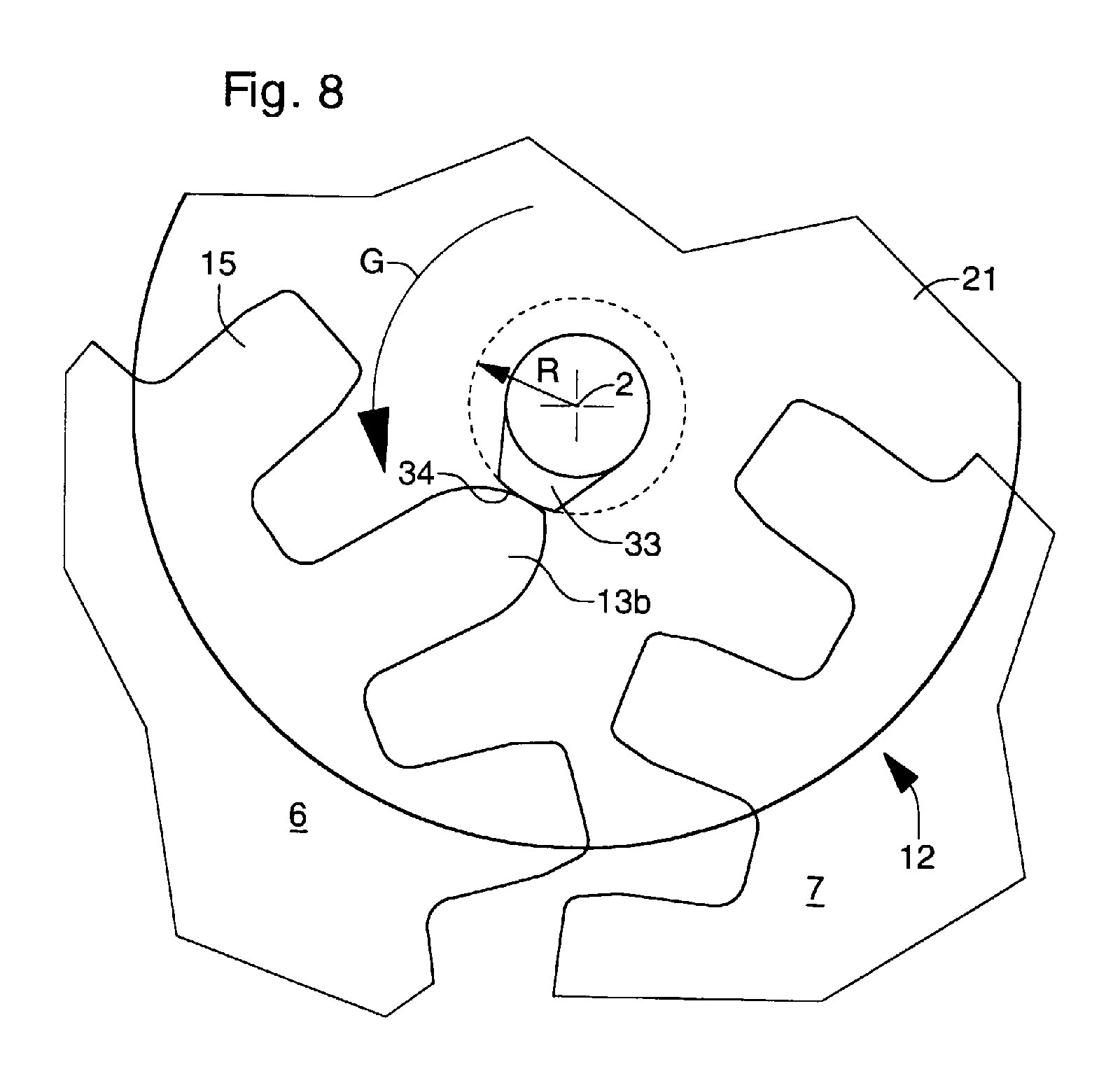
Detail of the teeth in the Dual Direct Escapement and the pivoting stopper. Source – European patent EP1041459A1
Unfortunately, the original design had some reliability issues that manifested themselves in early examples of the Freak, which tended to stop. A probable cause was the engagement of the rocking stopper with the protruding teeth – considering how far apart the protruded teeth are spaced out, the escape wheels need to sweep a relatively large distance per tick before contacting the stopper. This had a tendency to destabilise the rocker, which jams the escapement and stops the watch.
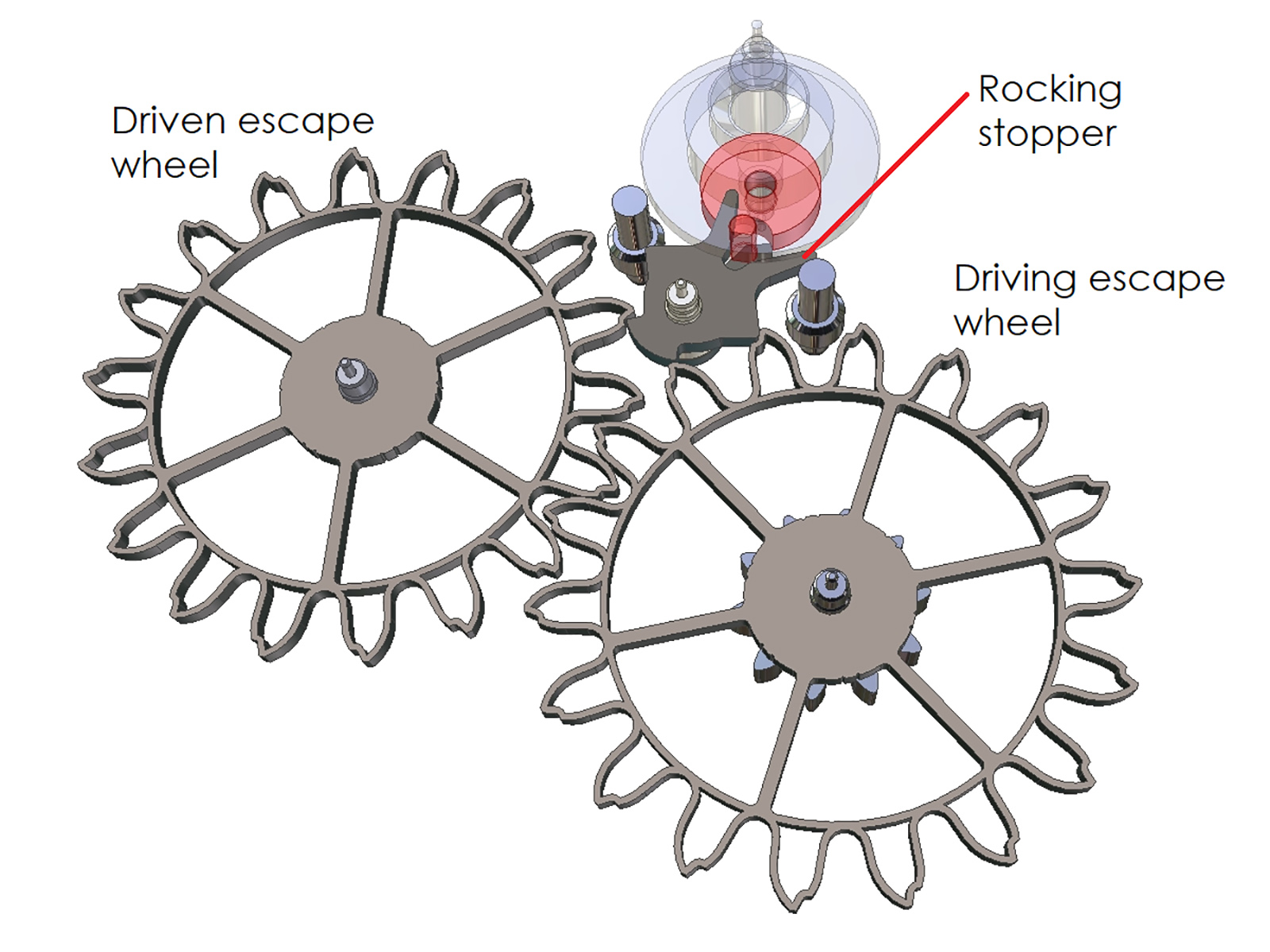
The Dual Ulysse Escapement. Source – Ulysse Nardin
A revised design, the Dual Ulysse Escapement, was then installed in the second generation watch of 2005, the Freak 28,800 V/h. The key difference were the redesigned escape wheels – while the first generation had only five protruding teeth per escape wheel, the new design had 18 identical teeth, all featuring a hooked tip reminiscent of a shark’s tooth, which nested on the edges of the redesigned stopper.
Since all of the teeth were now functionally engaging the escapement, it resulted in a smaller sweep angle per tick, yielding a more stable mechanism. It followed that since less time time is needed to rotate this smaller angle, the new movement incorporated a high frequency balance – hence the increase from 3Hz to 4Hz, or 28,800bph, explaining the model’s name.
With the introduction of the Freak, Ulysse Nardin pioneered not only the use of silicon, but also Breguet’s natural escapement on the wrist. And in a quirk of history, the Freak also had a distant link to Derek Pratt.
Pratt had entered his Double-Wheel Remontoir Tourbillon into the Prix Abraham-Louis Breguet, a watchmaking contest in 1997 held to commemorate the 250th anniversary of Abraham-Louis Breguet’s birth. Pratt, however, did not win. Instead, a young female watchmaker, Carole Forestier, now head of movement development at Richemont, clinched the award for her invention: a movement with its gear train and escapement on a carrousel that was surrounded by the mainspring. That formed the basis of the Freak, which was refined by Ludwig Oechslin, then the resident technical genius at Ulysse Nardin.
Voutilainen Double Direct Impulse Escapement (2011)
Another example of the natural escapement in independent watchmaking is the Voutilainen Double Direct Impulse Escapement, which made its debut inside the Vingt-8 wristwatch in 2011. It has a similar configuration to the F.P. Journe BHPE, and like other modern escapements, is possible due to advancements in fabrication technology.
At a glance, the case back reveals what appears to be a standard, high-end, time-only movement – with superlative finishing. But a closer look under the balance wheel reveals two blued escape wheels, the giveaway that it’s a natural escapement.
Interestingly, the pair of gears that drive the escape wheels are hidden under the base plate, on the dial side of the movement, so the escape wheels appear to be running mysteriously. This makes assembly more complicated, as the escape wheels and gears can only be fitted and adjusted after threading the pinions through the base plate. It’s also a small detail that allows Kari Voutilainen to showcase his watchmaking prowess.
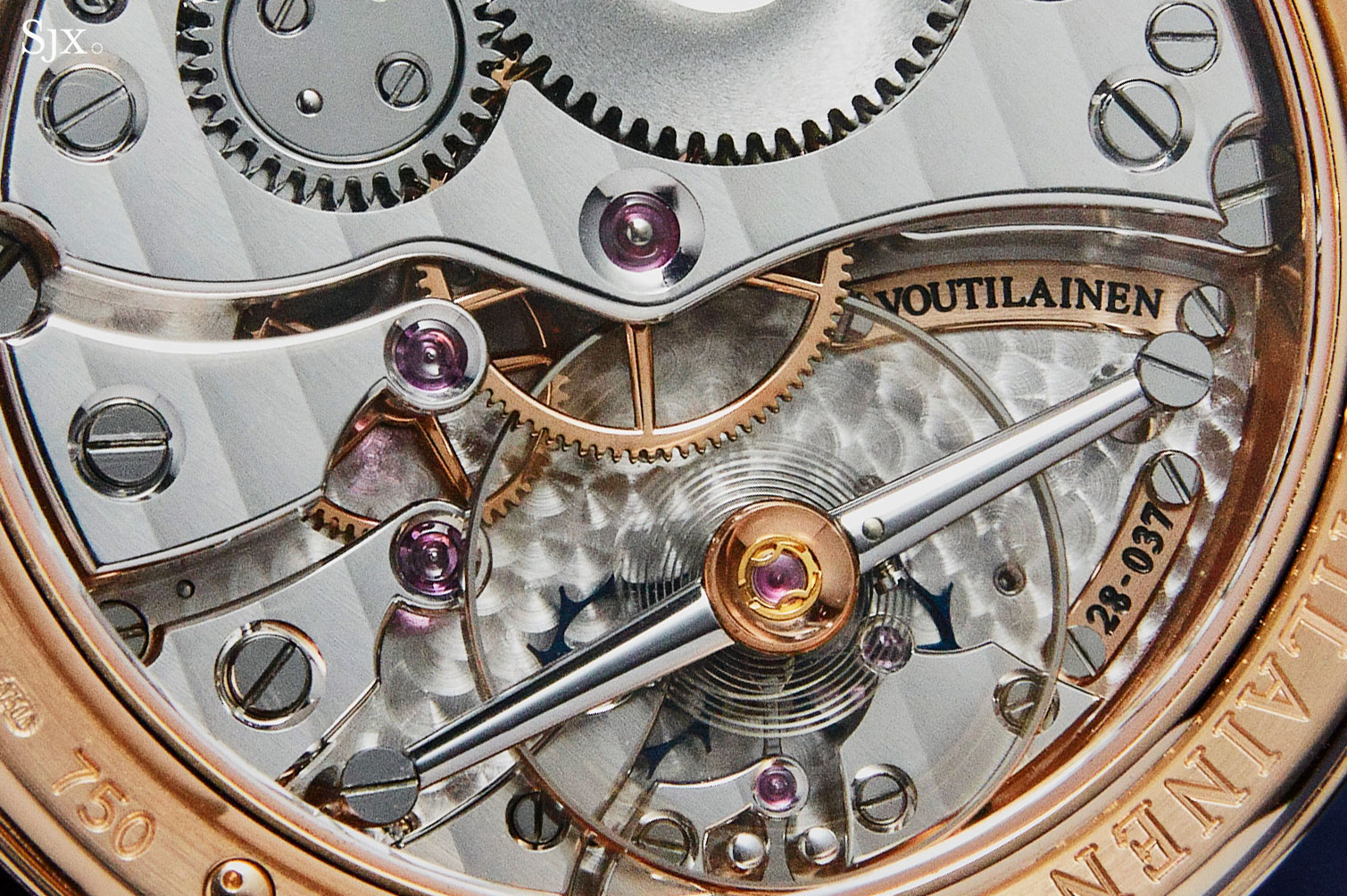
Only visible the escape wheels can be seen, with the gears that drive them hidden under the base plate
Also impressive is that no modern materials or processes, besides CNC milling, were utilised to achieve a working natural escapement. In fact, all the parts of the gear train are made of conventional materials like brass and gold, which also guarantees future serviceability. In the same vein, it is also unsurprising to find that the hairspring is eminently traditional, with a Breguet overcoil and Grossmann inner curve for better isochronism.
Laurent Ferrier Natural Escapement (2011)
Besides its signature tourbillon, Laurent Ferrier is best known for its Micro-Rotor movement, which was developed by movement specialist La Fabrique du Temps, now owned by Louis Vuitton. Though it is a three-hander, the movement is notable for a high degree of finishing, exemplified by the rounded anglage and black-polished bridge for the rotor. With all that visual complexity, it is less apparent that the movement incorporates a natural escapement.
The escapement relies on nickel-phosphorous parts that are the result of LIGA. Notably, the escapement is a close relationship of Breguet’s original design, and uses escape wheels with vertical teeth, or pillars. Thanks to LIGA, the wheels are fabricated from nickel phosphorus as a single part on two planes, simplifying the design and eliminating errors in assembly. In fact, the Laurent Ferrier escape wheel is probably the most faithful interpretation of the Breguet natural escapement.
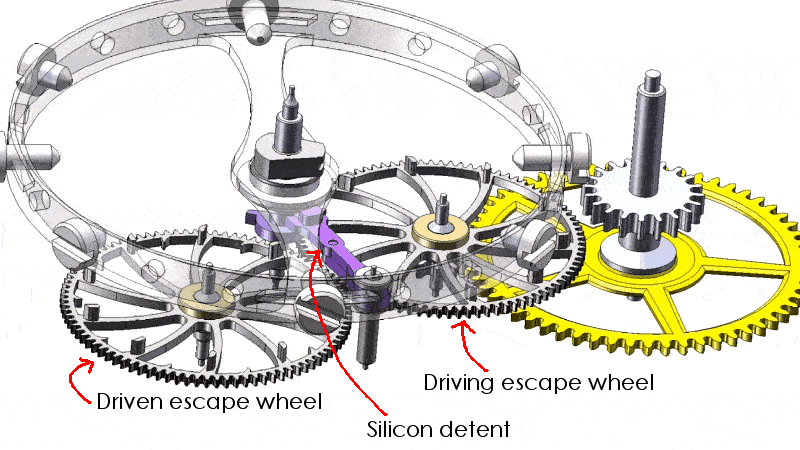
The Laurent Ferrier Natural Escapement. Source – Laurent Ferrier
In keeping with its largely traditional construction, the hairspring has a Breguet overcoil formed by hand, a detail that speaks of the craft within the movement. Nonetheless, the detent lever is made of silicon, giving it precise geometry with the required hardness and friction properties. Consequently, the detent lever is a single part, with no pallet jewels, which again, means less potential assembly errors. In fact, the detent is fabricated with an integrated guard pin, preventing accidentally unlocking of the escapement as a result of external shocks.
The caveat of the use of silicon is longevity: in the distant future, replacing complex, 3D silicon component might be challenging, as replacement parts cannot be made using traditional methods and instead have to be produced via DRIE or equivalent technology.
F.P. Journe Bi-Axial High-Performance Escapement (2012)
In 2012, F.P. Journe introduced the Chronométre Optimum, which was equipped with the patented Bi-Axial High-Performance Escapement (BHPE). Unlike in Breguet’s design, the escape wheels and gears in Journe’s invention are separate components. While this means the components are easier to fabricate, it requires careful adjustment so that the escape wheels are at the correct angle relative to each other, otherwise the mechanism stops.
As its name suggests, every aspect of the transmission system in the Chronométre Optimum was optimised for timekeeping performance – from the double mainspring barrels in parallel, to the hairspring with a Phillips terminal curve. But arguably most important is the remontoir d’egalité, which is the mechanism that supplies small controlled bursts of energy to the escapement from a small blade spring, a invention most famous for being found in the classic F.P. Journe tourbillon wristwatch.
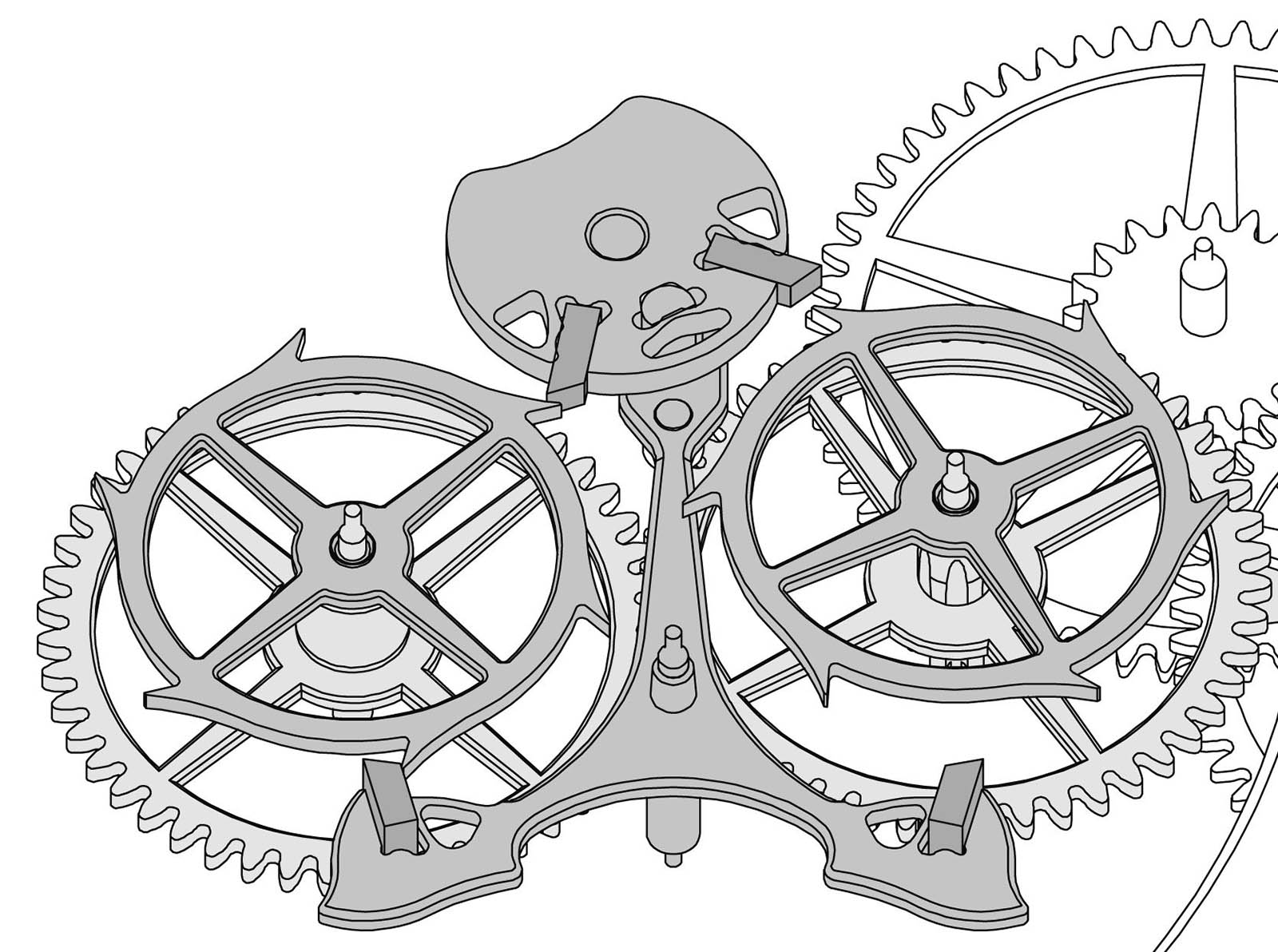
The escape wheels and detent lever are all made of titanium to reduce inertia. Source – F.P. Journe
Here the remontoir in the escapement acts as a buffer against the highest torque produced by the mainsprings when they are fully wound. In other words, the escapement only ever sees fixed, small doses of torque from the remontoir spring each second. This means that the natural escapement does not need to deal with high torque, which is beneficial for the operation of a delicate escapement and to control the backlash between the two escape wheels.
The low torque supplied to the escapement means that all its components are designed with low inertia in mind. Therefore, the escape wheels and detent lever are all made of titanium, the ideal material due to its lightness and strength. Traditional pallet jewels, four of them in fact, are used to engage the escape wheel teeth, with the detent carrying the first and second pallet stones while the balance wheel roller carries the third and fourth.
A quirk of the design is when the mainspring is nearly empty, the remontoir is disengaged entirely and the low-torque mainspring drives the escapement directly. This means the remontoir operates for the first 50 hours of the power reserve, with the remaining 20 hours being remontoir-free.
Girard-Perregaux Constant Escapement (2013)
The most unexpected and avant-garde interpretation of Breguet’s natural escapement is the Girard-Perregaux Constant Escapement. It’s worth noting that although the escapement is now owned by Girard-Perregaux, it was originally developed in the late 1990s by a watchmaker at Rolex, Nicolas Dehon. It was then named “Project ELF”, short for “echappement, lame, flambage”, or “escapement, blade, buckling”, which encapsulates the functional principles of the invention.
Though the idea was patented by Rolex, and several prototypes produced, it was never put into production, perhaps because the necessary materials and techniques for the escapement to work reliably were not yet available. About a decade after he first invented the escapement, Mr Dehon joined Girard-Perregaux, where his idea was finally realised.
Girard-Perregaux finally unveiled the wristwatch containing the escapement at Baselworld 2013. Within it was a good number of components in silicon – the secret sauce that made Mr Dehon’s idea possible – all produced in collaboration with CSEM. But as a result of various teething problems with the movement, the watch took several years to reach the market from its 2013 launch.
Despite its highly unusual appearance, the Constant Escapement is very much a natural escapement and operates on the same principles.
The Constant Escapement is made up of two escape wheels that look nothing like regular escape wheels. Unlike in Breguet’s design, the two escape wheels rotate in opposite directions, driven by the fifth wheel of the gear train.
An incredibly thin silicon blade, one sixth the width of a human hair, spans the butterfly-shaped silicon frame and is attached to the pallet fork at three points. This silicon blade buckles on every tick and tock, providing a constant impulse to the balance wheel each time, effectively isolating the varying mainspring torque, making this a true constant force escapement.
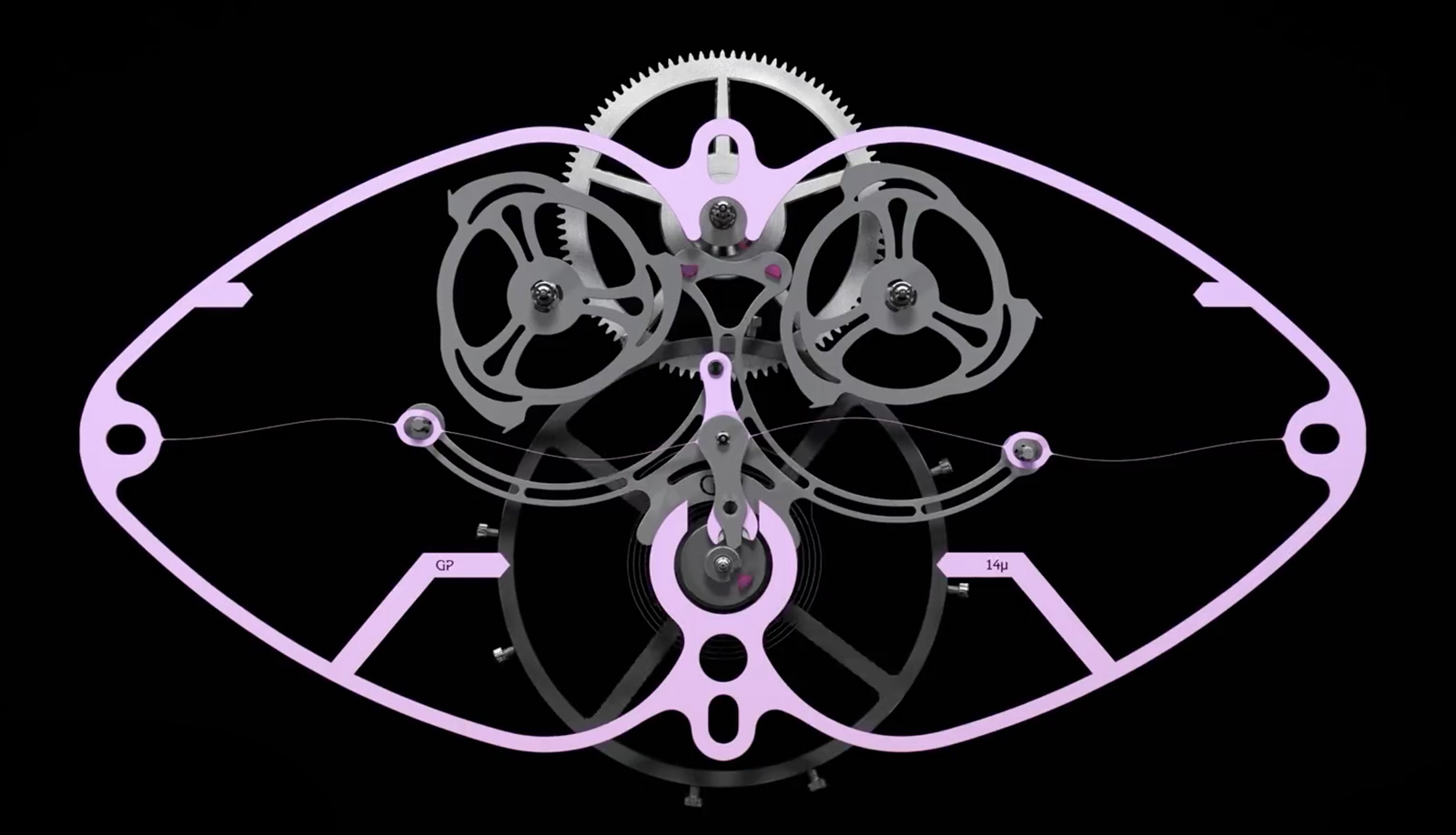
The Constant Escapement. Photo – Girard-Perregaux
Such buckling components are known compliant mechanisms, a field that is possible thanks to modern materials and production techniques. Favoured for their simplicity, compliant mechanisms can replace multi-part components, streamlining an otherwise complicated component into a single, jointless piece. Compliant mechanisms are found anywhere from household tools to even the safety and arming mechanism in a nuclear warhead. And beyond the Constant Escapement, compliant mechanisms are also found in other movements, and need not be in silicon. The most prominent example is the Patek Philippe Aquanaut Travel Time ref. 5650G “Advanced Research”, which uses a compliant mechanism for the second time zone adjustment.
The Constant Escapement, however, demonstrates the vast potential of silicon compliant mechanisms in watches. Though still in its infancy, such mechanisms would likely eventually become more widespread as technology progresses, at the same time making the creation of replacement parts more feasible.
Charles Frodsham Double Escapement (2018)
Last year, Charles Frodsham unveiled a traditional approach to the natural escapement in the form of the Double Impulse Chronometer wristwatch. Sixteen years in the making, the watch pays tribute to the works of Breguet, Daniels and Pratt.
The basic idea is simple, and is perhaps the most direct modern interpretation of Breguet’s natural escapement. Like the George Daniels Space Traveller, the Frodsham movement has separate gear trains powering each escape wheel, making it the first ever to miniaturise Daniel’s double-train construction into wristwatch size.
The central titanium detent serves only to lock the two escape wheels. Impulse is given in alternate cycles to the balance by the escape wheels, and since both are independently powered, there is no play or backlash present, which allows the design to operate without going out of sync and freezing.
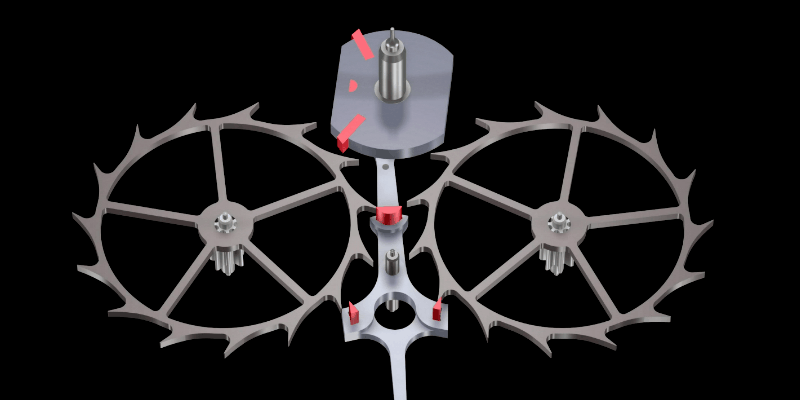
The double escapement in action. Notice the escapement wheels rotate in different directions as they have separate, independent gear trains. Source – Charles Frodsham
However, there are a few challenges inherent in the construction, making it a tremendously difficult watch to put together, despite being time-only. As with the Space Traveller, it is effectively two movements in watch, thus requiring twice the number of wheels and pinions, resulting in a largish, 42.2mm case.
More subtle is the complexity of the power supply. To be certain that the torque delivered by each mainspring to its respective escape wheel is equal, the pair of mainsprings in each movement are matched for parity. To further ensure one train doesn’t run down before the other, a balance brake is employed, and engages after 36 hours of running time. Stopping the balance wheel, and hence the power flow from the mainsprings, keeps the escape wheels locked positively on the detent jewels. The brake automatically releases once the watch is fully wound.
Given its historical inspiration, it is expected that gear train parts in the Double Impulse Chronometer are made of conventional metals. The wheels are made of 18k rose gold with tempered steel pinions, while the detent and escape wheels are made of titanium for lightness. Meanwhile, the balance wheel is a temperature-resistant copper alloy with tungsten carbide adjustable weights. This is a convincing formula for longevity and serviceability.
Concluding thoughts
Abraham-Louis Breguet’s dream of the natural escapement was truly ahead of its time; it took more than two centuries for materials and production techniques to catch up with his invention.
That being said, the precision required for a reliable natural escapement still makes it difficult to implement on an industrial scale, even today. Of all of the escapements above, only the Ulysse Nardin escapement is produced in substantial numbers. And credit for that goes to a farsighted investment by Ulysse Nardin in 2006, when it set up Sigatec, a manufacturer specialising in both DRIE and LIGA, in collaboration with Mimotec.
And even then, the quantities produced are tiny in the grander scheme of things – Ulysse Nardin produces perhaps 20,000 watches a year, compared to almost a million at Rolex and nearly as many at Omega. In fact, Omega is the only watchmaker producing large volumes of watches with anything other than the traditional Swiss lever escapement, having replaced it with Daniels’ Co-Axial escapement.
But as technology continues to evolve, who knows what the future holds for Breguet’s idea? Alternative materials or fabrication processes may make new variants of the natural escapement, or perhaps even industrial production possible.
Correction August 22, 2019: Omega does not make a million watches a year, but almost that number.
Back to top.