In-Depth I: Grand Seiko Kodo Constant-Force Tourbillon SLGT003
A very different and very impressive Grand Seiko.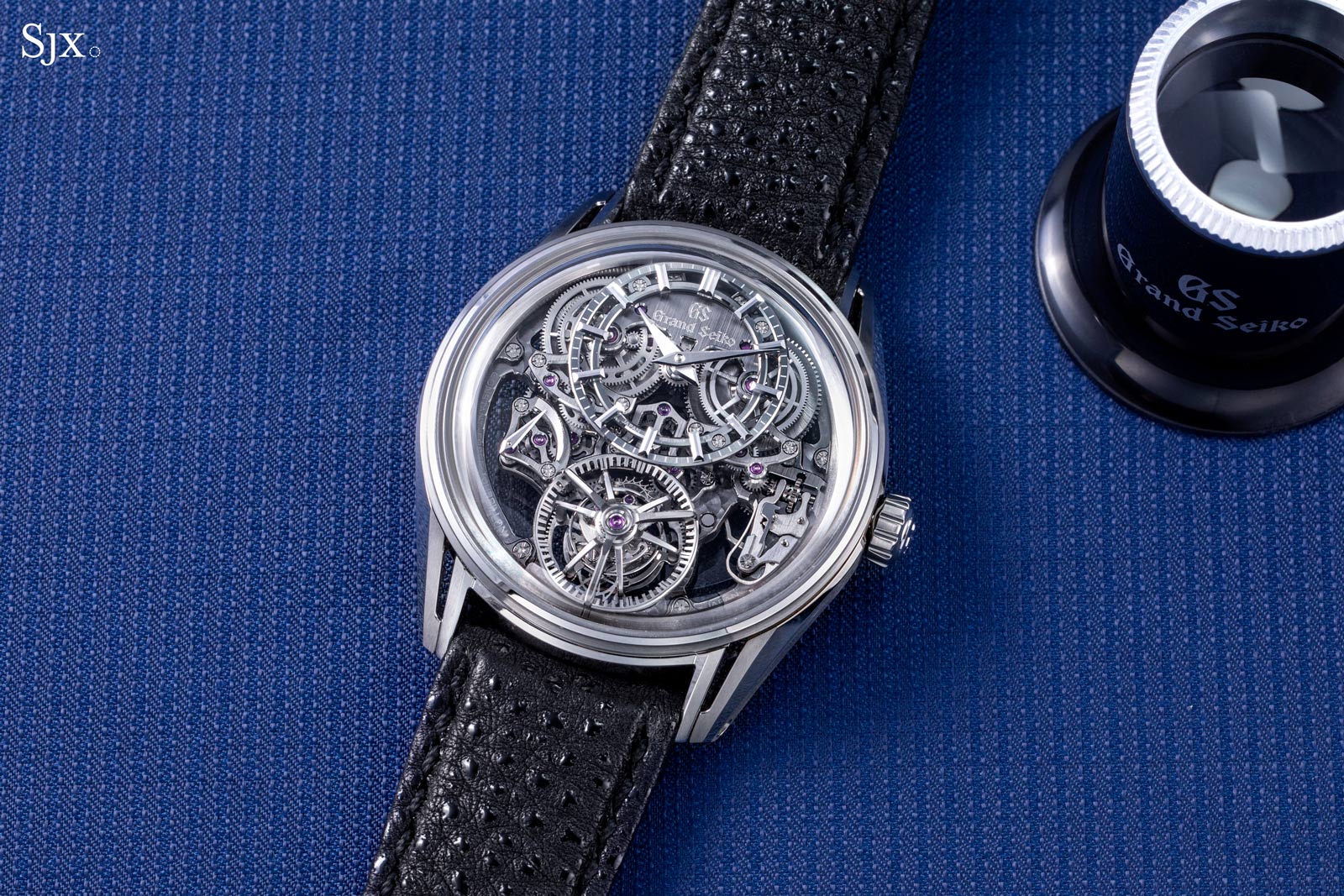
The first complicated mechanical watch from the brand in its six decades years of history, the Grand Seiko Kodo Constant-Force Tourbillon SLGT003 is an impressive example of high horology. The Kodo is self-explanatory: it is equipped with a highly skeletonised and sensitively finished movement boasting a one-second remontoir and tourbillon, both mounted on the same axis.
The Kodo is an interesting watch in all respects, tangible and intangible, making it worth a detailed examination – exactly the focus of this two-part series. In this first instalment, we explain the development and conception of the Kodo, as well as the decoration of its movement. In the second part that will be published subsequently, we detail how the movement works and analyse how it compares to the competition.
A surprise
Evolved from the T0 concept movement unveiled just two years ago, the Kodo is undoubtedly a milestone – and a major step upwards – for the Japanese watchmaker that’s historically been focused on simple but high-quality everyday watches. Like conventional Grand Seiko (GS) watches, the Kodo is all about high-quality timekeeping, but it is far from simple.
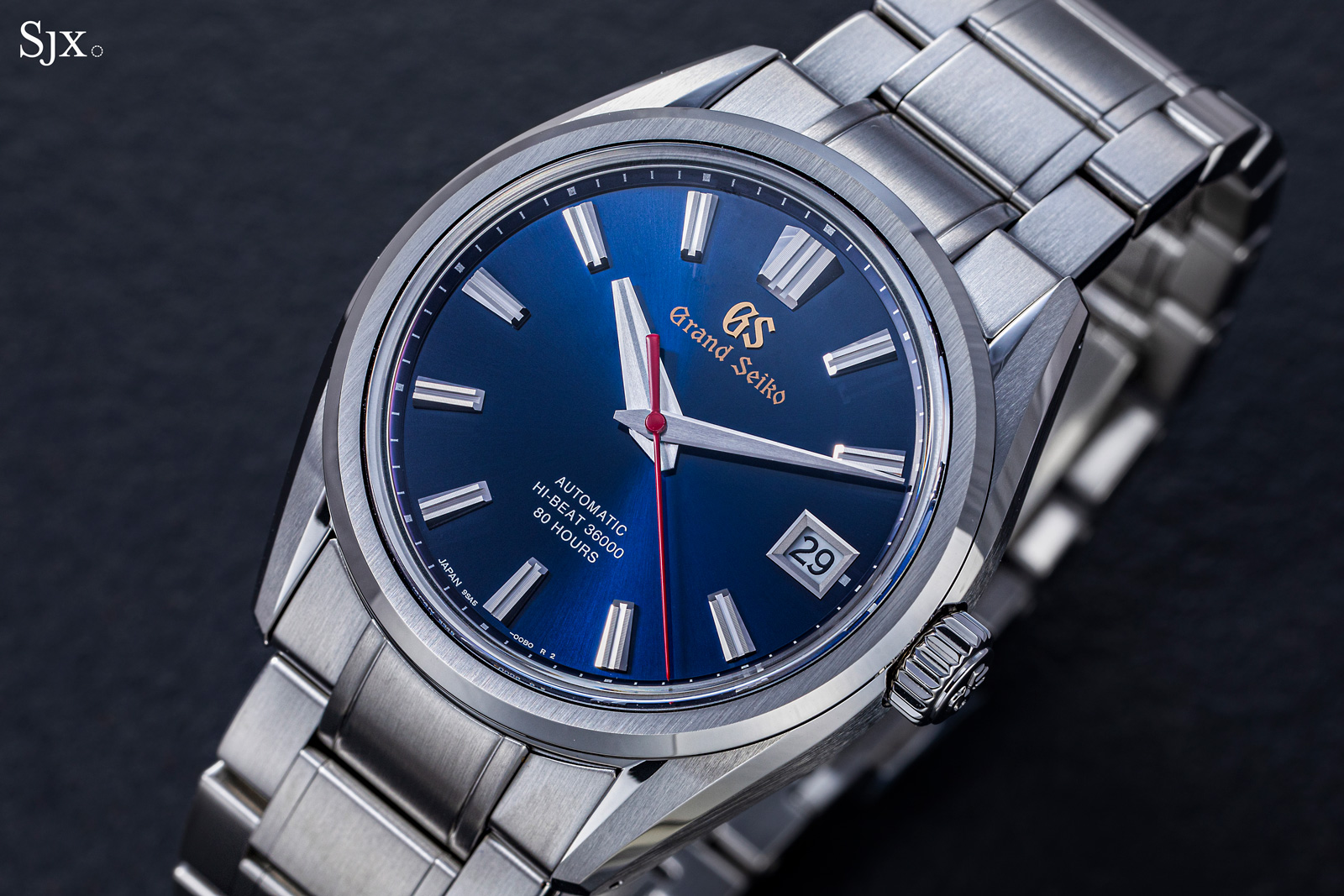
An example of a typical Grand Seiko, which is strikingly different from the Kodo, yet not so different in terms of philosophy
Well known for its quest for high precision – amongst its earliest timepieces were observatory-tested chronometers – GS has done much research and development in the cutting-edge timekeeping technologies other than mechanical, including quartz and its proprietary Spring Drive. Now an established brand with strong development and manufacturing capability, GS often utilises modern materials and techniques, such as nickel alloy wheels made via lithography. And the Kodo goes even further, being the first GS to have ceramic wheels.
The Kodo continues that decades-long quest for precision, but is instead rooted in traditional solutions to chronometry. It’s a return to nuanced, mechanical systems rather than high-tech materials such as silicon. This traditional approach makes the Kodo an unexpected creation from a mainstream brand, given such esoteric watches are typically the work of niche or independent watchmakers.
Another highlight of the Kodo are its tangible technical qualities. One obvious highlight is the construction of the constant-force mechanism and tourbillon. The constant-force cage contains the tourbillon cage, but both rotate on the same axis. Already a rare combination of complications, it’s even rarer that the two mechanisms are constructed in a co-axial manner.
Another is the fact that the Kodo is a skeletonised watch, resulting in a movement is practically see-through. While the Kodo is the first-ever skeleton GS, it does build on an in-house expertise as Seiko does offer a variety of hand-made skeleton movements under the Credor label.
Initial thoughts
The result of ten years of development – done entirely in-house without on external specialists – the Kodo represents an impressive culmination of GS’ watchmaking prowess. It is also notable because it’s unusual for a large brand that mostly concentrates on affordable watches to venture out of its comfort zone and invest resources in creating something this exotic.
In typical GS fashion, the Kodo is rigorous in its technical execution and best described as a chronometrically-focused mechanical treat. The tourbillon and remontoir together is a rarity that is historically the preserve of respected independent watchmakers such as F.P. Journe. But the Kodo does one better by integrating the remontoir into the tourbillon with a pair of co-axial cages. While the overall concept is not a historical first, the movement has few peers and certainly ranks amongst the most accomplished.
The design might be controversial because it departs significantly from the familiar GS aesthetic. Admittedly, I didn’t warm to the design when I first saw photos of it, but the hyper-mechanical style makes sense when I examined the watch in the metal. The Kodo has a complex and intricate appearance that is paradoxically visually light; its aggressively mechanical design elements are elegant in their own way.
In the hand, the watch is stunning, both for the incredible detail but also in how the movement components gleam in the light. The reflective and dark movement components were evidently conceived to maximise the interplay of light and shadow, a principle that GS proclaims to utilises across its designs. But whereas that depends on the surfaces of external components like the hands and dial in a typical GS watch, the Kodo transforms the movement into a stage where light and shadow dance.
Priced at US$350,000, the Kodo is the most expensive GS watch ever, far surpassing the brand’s previous record holders that pricey because they were high-jewellery timepieces. But the big number is the natural and reasonable consequence of its mechanical complexity. More pertinently, the price is within the ballpark for comparable watches by both independent and establishment brands.
Importantly, the appeal and value of the Kodo goes beyond its tangible qualities – it is a historically significant watch, being the first of its kind by an Asian watchmaker.
Aesthetics
Though magnificent in technical terms, the Kodo is nevertheless controversial in terms of design, at least in the eyes of traditionalists. That’s because the Kodo is unlike any other GS. Instead it goes all out to showcase its mechanics via a movement that’s entirely open-worked and centred on the large, nested cages of the remontoir and tourbillon. This makes the Kodo both the first GS with a tourbillon as well as the first skeleton.
Admittedly I was a little sceptical when I first saw the stock images of the watch, but I changed my mind as soon as I laid eyes on it during Watches & Wonders (W&W). Characterised by a highly mechanical appearance, the watch is strikingly intricate but avoids being loud or messy. It’s difficult to sum up why exactly the Kodo is attractive, but it is.
Since the people behind the watch were present during the presentation at W&W, I quizzed them about the origins of the design.
It turns out one of the key aspirations behind the Kodo’s aesthetic is familiar, having been applied to more conventional GS watches. That is the contrast between light and shadow, typically exemplified by the multifaceted and impressively finished hour markers and hands found on every GS watch. Found only on the case and dial in ordinary GS timepieces, the interplay between light and shadow has been extended to the movement in the case of the Kodo.
While the use of reflections and light is familiar to GS, the Kodo interprets the concept in a modern manner, albeit in a way that remains Japanese. The brand refers to the design approach as seeking airiness, which is self-explanatory given the see-through nature of the movement.
This was achieved by first open-working the movement components and constructing the calibre in layers, a process that required both the watch designer and movement constructor to work in sync. The result manages to capture the light, shadow, and everything in between, creating a dynamic, nuanced mechanical landscape despite the monochromatic finish.
As the creators of the Kodo explained its origins, it dawned on me that the themes that informed the design of the Kodo are exemplified by a handful of notable details. The first is the monochromatic palettes that’s just shades of grey, which serves to dial down down the visual complexity while giving it a more refined appearance. This is especially obvious when the Kodo is compared against the T0 concept movement that was dressed in blue, gold, and grey.
The next detail concerns the dial for the time that’s made up of a chapter ring carrying hour markers. It creates a focal point for the wearer that lets the rest of the movement recede into the background. Along with the tourbillon at six o’clock, the sub-dial unites the densest sections of the movement, creating a good contrast with the transparent sections below.
Another is the case of the Kodo. Skeletonised just like the movement, the case is a twin-alloy affair made up of a platinum inner case contained within an outer case of Brilliant Hard Titanium. The two-part construction utilises the harder titanium alloy to protect the softer precious metal within (however, the pictured watch is the prototype that has a case entirely in German silver).
The resulting watch looks nothing like a typical GS and is surely polarising. But as was my experience, seeing it in the metal and then coming to understand the rationale behind its development certainly helps to form a positive impression. Despite its unorthodox aesthetics, the Kodo is entirely understandable as a product. Being the first ever highly complicated GS, it has to stand out and it certainly succeeds.
That said, I still look forward to seeing some equally technically complex in a more restrained and classical package, something that is quintessential GS. That would certainly appeal to the purist GS enthusiasts.
From T0 to 9ST1
Unveiled in 2020, the T0 concept movement was the starting point for the cal. 9ST1 in the Kodo. Though the two are similar in construction, they are entirely different movements. Both have different diameters and thickness, with the cal. 9ST1 being smaller and thinner in order to fit inside a wearable wristwatch. To understand how the T0 led to the cal. 9ST1, we spoke with Takuma Kawauchiya, the watchmaker who constructed the Kodo and its movement.
“In developing the 9ST1 from the T0, design changes were made from various perspectives,” says Mr Kawauchiya, “[It went beyond] miniaturisation, and more than 90% of the parts were redesigned.”
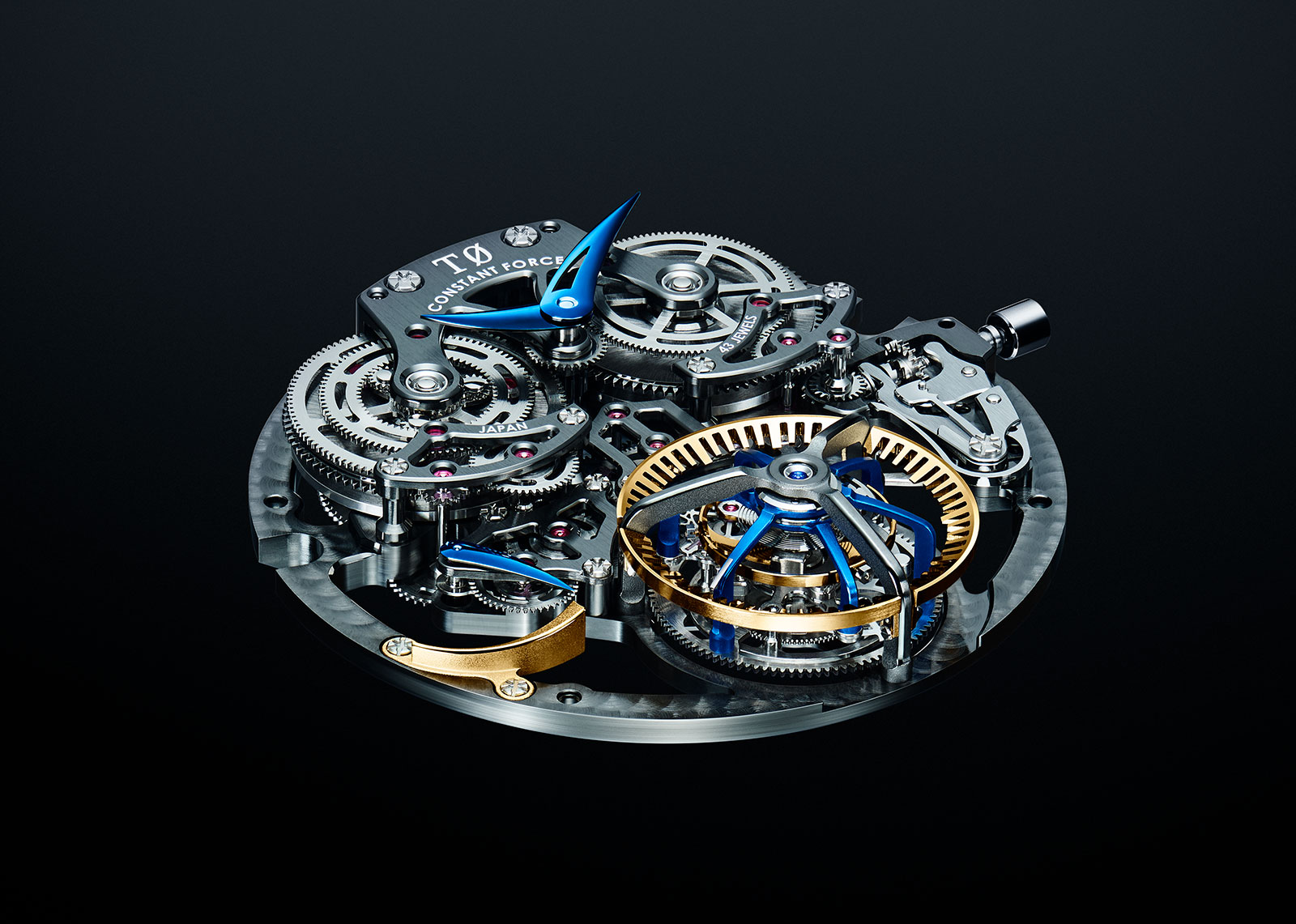
The T0 concept movement of 2020. Image – Grand Seiko
“When we decided to commercialise T0, Yu Ishihara, the watch designer, first designed a case for the T0 movement just as it was, and then made a mock-up using a 3D printer to verify the physical design,” continues Mr Kawauchiya.
“As a result, we concluded that the movement needed to be smaller in order to achieve perfect wearability and the ideal degree of freedom in design,” adds Mr Kawauchiya, “Ishihara and I discussed various ways to reduce the size of the T0 without changing its basic layout, and we made major changes mainly in the layout of the power reserve train and the structure of the carriage bridge.”
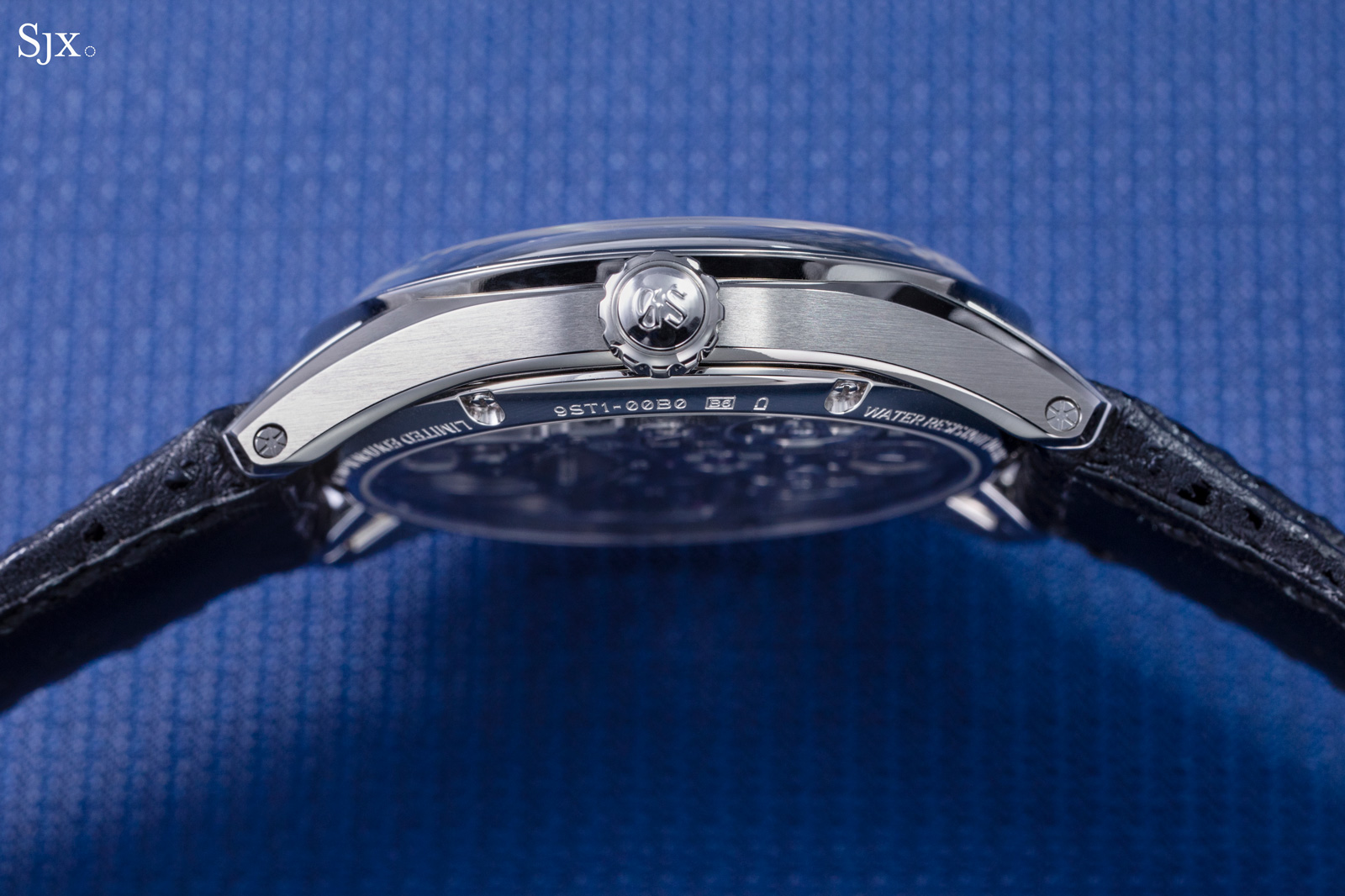
Despite its complexity, the Kodo is surprisingly thin, a quality that is obvious when observing its profile
Though the overall arrangement of the key parts of the movement remain unchanged from the T0 to the cal. 9ST1, many details were subtly altered as a result of the redesign. Amongst them is the power reserve indicator, which remains in a similar position but with an entirely different orientation.
“For the power reserve train, Ishihara edited the CAD model of the movement and proposed a new approach, something no other designer can do,” says Mr Kawauchiya.
“Based on Ishihara’s suggestion, we made the design into details and added a new bridge with a power reserve indicator, Mr Kawauchiya continues, “As a result, the power reserve indicator was turned inward, reducing the outer diameter of the movement and preventing legibility loss due to the curve of the crystal.”
As for the gigantic carriage at six o’clock, Mr Kawauchiya says, “The carriage arm at six o’clock in particular was an obstacle in reducing the outer diameter of the movement.”
“Ishihara and I considered several patterns in changing the structure of the three arms of the carriage, but we could not find a shape that was more beautiful than the three arms,” he explains, “In the end we decided to keep it as it is and make the movement as small as possible.”
“Since it was difficult to make the carriage smaller than that in the T0, we accomplished this by reducing the thickness of the carriage bridge, downsizing the seconds index, and changing the arm fixing structure,” explains Mr Kawauchiya.
But scaling down the movement was not merely an exercise in reduction. It had to be done while maintaining a high level of shock resistance. “The challenge was to make the parts thinner and smaller while meeting the shock resistance required for Grand Seiko,” says Mr Kawauchiya, “We conducted numerous drop tests to find a structure that was as thin as possible while maintaining strength.”
Mr Kawauchiya is particularly proud of the movement’s robustness, “As a result, Kodo’s diameter was reduced from 36.3 mm of T0 to 35.0 mm, while still passing drop tests and other impact resistance tests.”
Interestingly, Mr Kawauchiya points out the similarity between the cal. 9ST1 and the high-beat cal. 9SA5 that was also unveiled in 2020 to mark the 60th anniversary of Grand Seiko.
“In order to stabilise the accuracy of the balance, we adopted the screwed balance developed for cal. 9SA5,” says Mr Kawauchiya. But the influence of the cal. 9SA5 on the cal. 9ST1 is arguably more obvious in the decorative aspects of the movement.
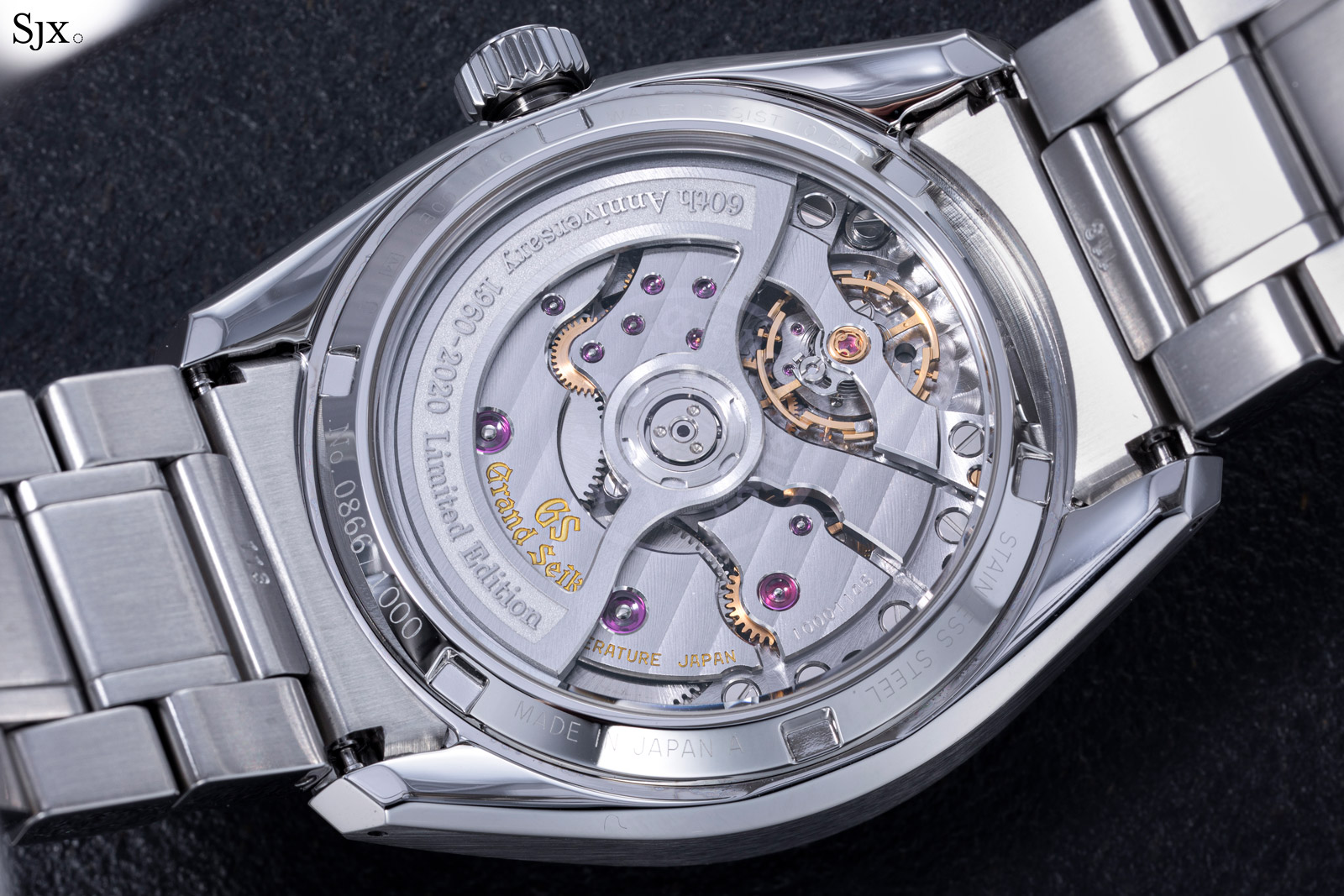
The 9SA5
Finishing
“Based on our experience with the T0 and cal. 9SA5, we also focused on the following three points for a more pleasing appearance,” says Mr Kawauchiya, referring to the aesthetics of the movement.
“First, the chamfer of the main plate and the bridge is 0.05 mm wider than that of the T0 to give the movement a deeper appearance. Second, nine different types of hole jewels were newly designed to match the 9ST1 movement size, paying attention to the outer diameter, thickness, and even the size of the oil reservoir,” explains Mr Kawauchiya.
“Third, the angle and direction of the grinding wheel were also designed to minimise the steps in order to achieve the most beautiful wave pattern finish [also known as circular Côtes de Genève]. In order to minimise the amount of grinding, the inclination of the movement is adjusted in the order of microns while applying the wave pattern finish.”
All of that incredible attention to detail can only be appreciated under magnification. In fact, the finishing of the cal. 9ST1 might seem ordinary at a glance, but it is surprisingly unique up close. Instead of the usual decoration typical of high-end Swiss brands, the cal. 9ST1 is finished in a manner that distinctively GS.
In fact, the style of decoration brings to mind standard GS movements, except that those are decorated in an industrial manner. The cal. 9ST1, on the other hand, is finished by hand in an artisanal manner.
A closeup inspection reveals that the finishing is impressively well done. The decoration is so fine that the watch catches the light even at arm’s length thank to numerous mirror-polished surfaces within the movement.
And it’s not just the quality of the decoration, but the magnitude of it. Because the movement is extremely skeletonised – you can see right through the watch at some points – the sheer surface area that requires decoration is vast, making the thoroughness of the finishing even more admirable.
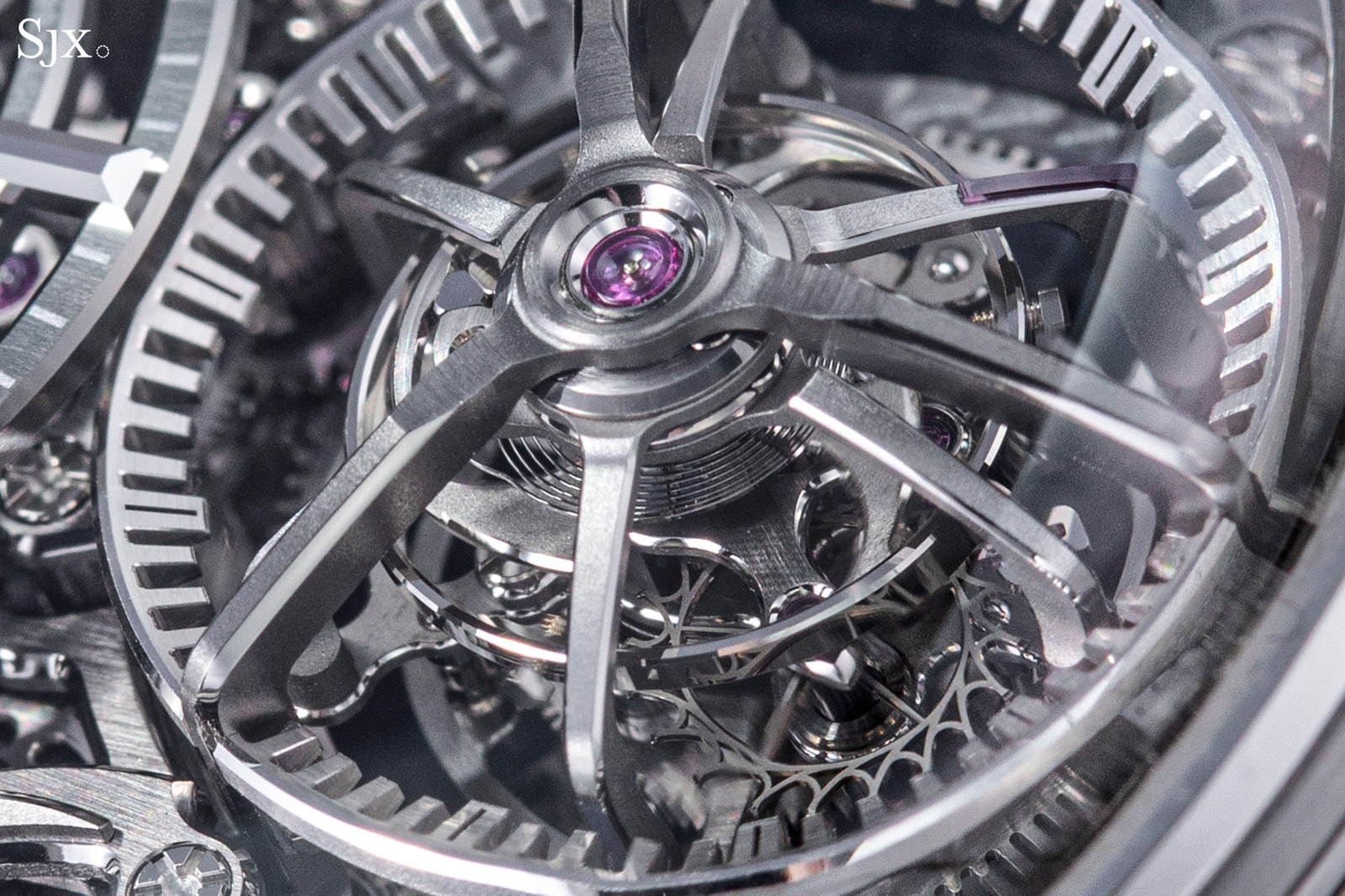
The balance wheel is polished and beveled on both the front and back
One of the most notable aspects of the decoration is the bevelling, which is done at an almost 45-degree angle, instead of the rounded anglage favoured by Swiss watchmakers. These flat bevels – which are evidently finished by hand – suit the contemporary, mechanical aesthetic of the watch well.
Interestingly, though most of the bevelling on the bridges is flat, other components still sport the a more traditional European type of finishing. Rounded, polished bevelling can be found on several smaller components visible on the front and back.
The decoration is also paradoxical in a manner that sets it apart from its peers – and perhaps reflects the no-expense-spared approach to quality that is recognisably Japanese. While most movements have finer finishing on bigger, easier-to-see parts, the Kodo instead has more elaborate finishing on its smaller components. The smallest bridges, for example, have rounded bevelling, which is apparent on the bridge for the the remontoir as well as slender bridges under the dial.
The thoroughness of the finishing is evident in parts that are even smaller – and that holds true for even some unexpected components. For instance, the unique six-slot screws are chamfered on all interior and exterior edges. Each screw is an achievement in itself considering there are 12 inner edges along the six slots, as compared to just two edges for a conventional slotted screw – and dozens of screws within the movement.
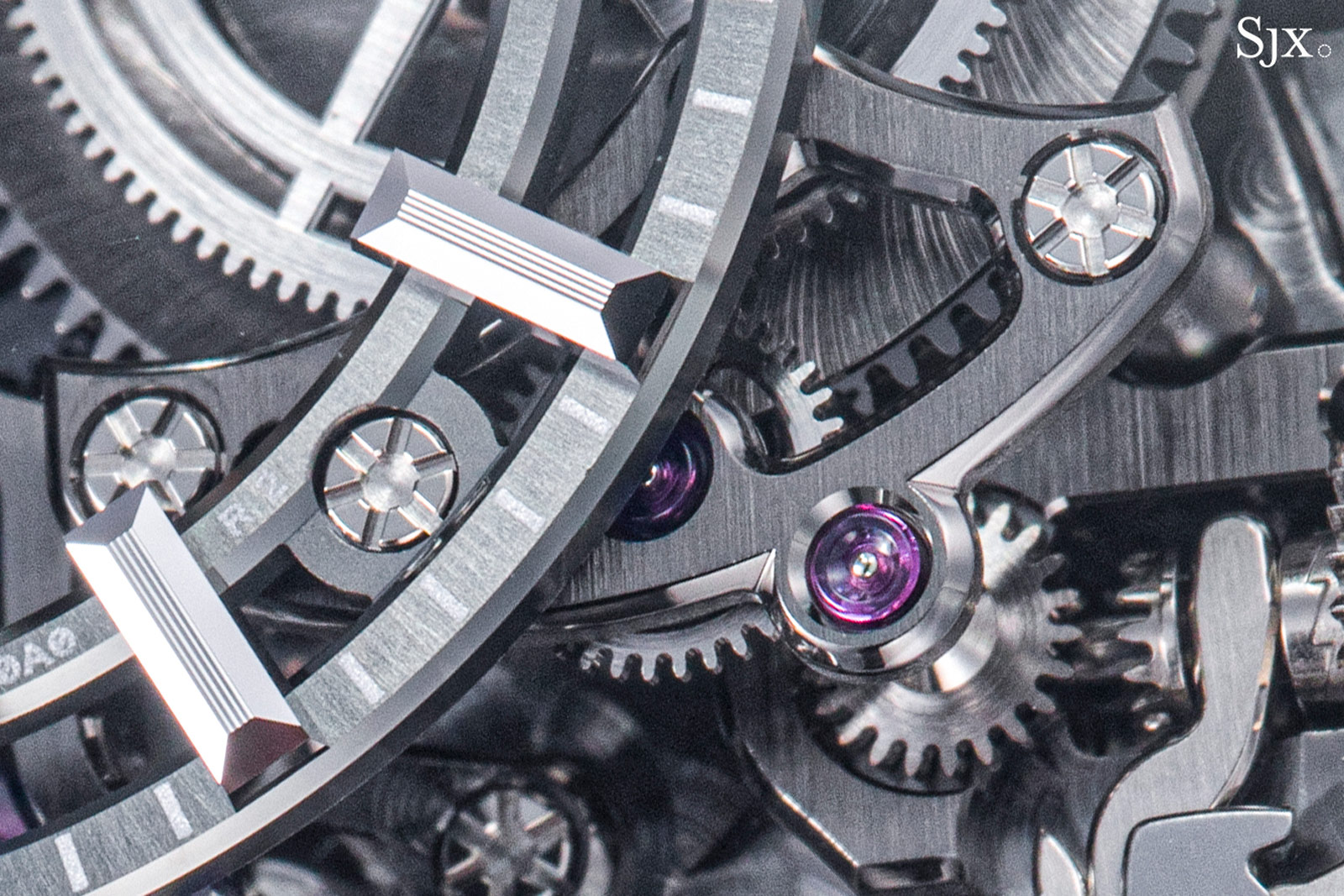
The bridge at one o’clock even has sharp inward angles along its edges
The past and future
Evidence of the past – and possibly the future – of the Kodo were on show at W&W and they were certainly intriguing. Take for instance the prototype movement exhibited in the Grand Seiko’s booth that was entirely different in shape – it was an oblong, form movement – but incorporates the same tourbillon and remontoir found in the Kodo.
“This prototype allowed us to confidently set a direction and begin designing the T0,” says Mr Kawauchiya, “It is a very memorable movement for me.”
“The oblong prototype movement was one of the very earliest prototype made the year after I came up with the mechanism in 2012, and it was my first experience designing a movement of any kind,” explains Mr Kawauchiya.
“[The oblong movement] was the first job for me and Ishihara. In order to shorten the development period of the Kodo, we used parts from existing movements as much as possible, but I asked Ishihara to join as a designer because I wanted the appearance of the prototype to be as beautiful as possible, even if it was only for internal presentation. You can already see in this prototype elements that would lead to the T0 and 9ST1, like the colours for example.”
“With this prototype, we were able to confirm that a constant-force tourbillon as one unit on a single axis could achieve high precision, leading us to see the potential in the sensual value of the 16-beat rhythm [of the balance],” adds Mr Kawauchiya, “And the use of ceramic for the stop wheel was also an idea that came from this prototype.”
The Kodo also points to where GS is going.It’s worth mentioning that the watch was developed by an elite group of Grand Seiko’s watchmakers and designers who will be part of the Atelier Ginza, a recently-established workshop located in Tokyo that is separate from the Micro Artist Studio in Shiojiri, traditionally the origin of the highest-end watches of the Seiko Group brands.
“Atelier Ginza is a place where you can experience the craftsmanship of the Seiko Group,” says Mr Kawauchiya, “Our founder, Kintaro Hattori, believed that ‘Good products always win the patronage of consumers’.
“Atelier Ginza inherits this strong belief and it is a place where the best craftsmen and women and designers aim to create watches that are unparalleled in their craftsmanship,” he adds, “And it is in Ginza, the district where Kintaro Hattori founded Seiko.”
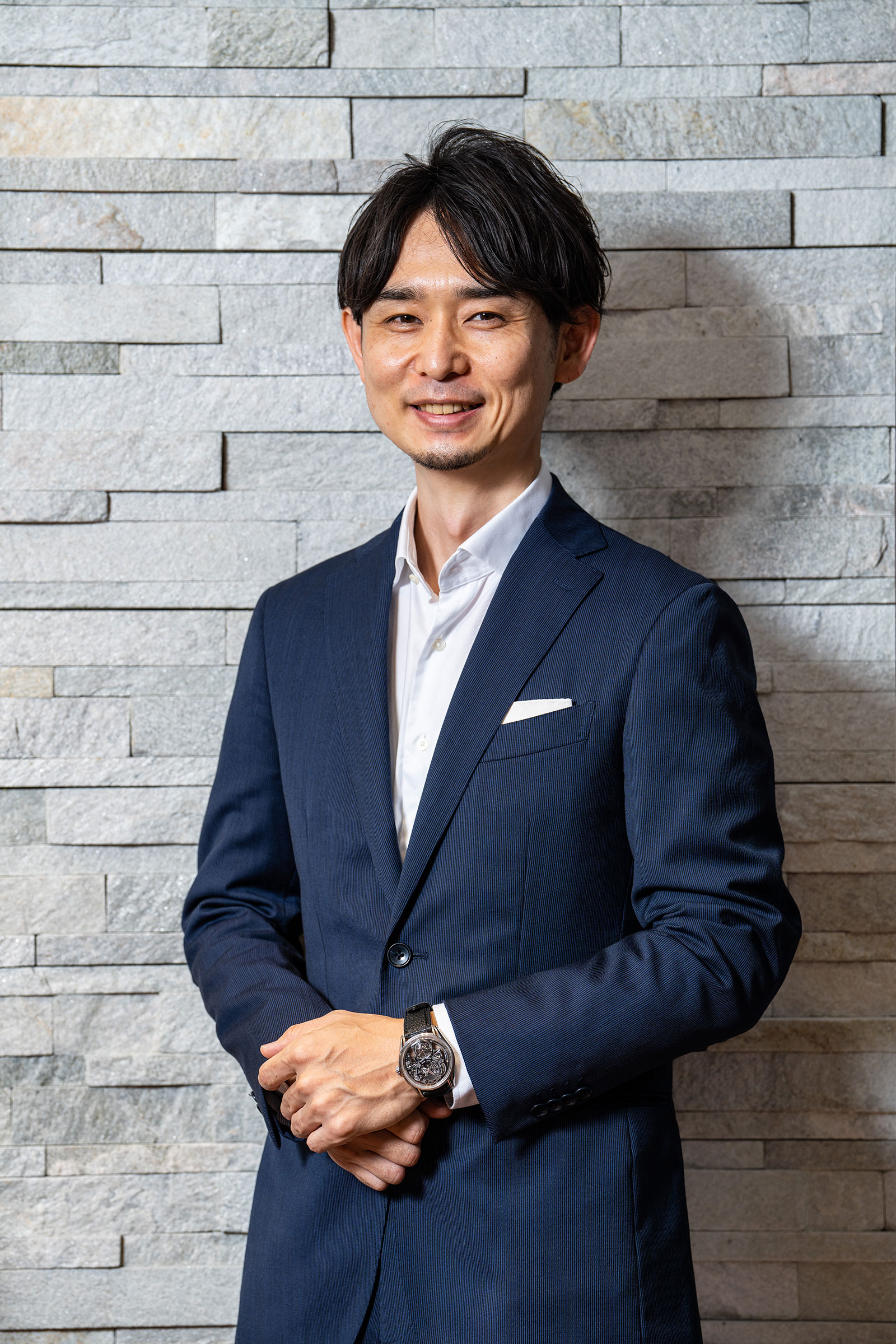
Takuma Kawauchiya wearing the Kodo. Image – Grand Seiko
Finally, I noticed that the constant force mechanism inside the Kodo is protected by Japanese patent JP2015072254A of 2014. But there was another patent filed two years later in Switzerland, CH710863B1, which appears to be an extension of the original constant force construction but instead applied to a multi-axis tourbillon.
When asked to comment on the Swiss patent, Mr Kawauchiya is enigmatic. “Thank you for taking a look at our patent. It was a very natural idea for me to apply the original one-unit, single axis structure to multi-axis carriages,” he says, “However, it only means that we have applied for such a patent, and unfortunately I cannot tell you about our future plans at this moment.”
Conclusion
The Kodo Constant-Force Tourbillon is an ambitious watch, but it is executed to the highest level. It demonstrates a high level of attention to detail from construction to decoration, while also reflecting the manufacturing prowess of the Seiko Group, a feature that sets it apart from other watchmakers in this segment, most of which are smaller-scale operations.
In addition to its technical qualities personified by the remontoir and tourbillon, the Kodo demonstrates the brand’s courage in reimagining its design language. The result might not be for everyone – there will only be 20 examples of the Kodo in any case – but it is notable that the brand is venturing into territory, especially since GS has historically been conservative in terms of design.
Along with Atelier Ginza, where according to Grand Seiko “an elite group of watchmakers and designers will gather to create world’s finest watches”, the Kodo is a sign that GS is serious about mechanical haute horlogerie. It is certain that the Kodo will not be the last high-end mechanical complication from GS.
Key facts and price
Grand Seiko Kodo Constant-Force Tourbillon
Ref. SLGT003
Diameter: 43.8 mm
Height: 12.9 mm
Material: 950 platinum and Brilliant Hard Titanium
Crystal: Sapphire
Water resistance: 10 bar
Movement: Cal. 9ST1
Functions: Hours, minutes, dead-beat seconds, tourbillon with constant-force mechanism
Winding: Manual wind
Frequency: 28,800 vibrations per hour (4 Hz)
Power reserve: 72 hours
Strap: Calf strap with platinum folding buckle, and additional double-sided crocodile strap
Limited edition: 20 pieces
Availability: Starting October 2022 from Grand Seiko’s retailers and boutiques
Price: US$350,000; or 40 million Japanese yen before tax
For more, visit grand-seiko.com.
Back to top.